Nuovi progetti di ricerca per le costruzioni metalliche relative al mese di luglio 2024
Nuovi progetti di ricerca per le costruzioni metalliche relative al mese di luglio 2024
Nel mese di luglio 2024, in Italia è stato dato il via a un ampio ventaglio di nuovi progetti di ricerca e normative nel campo delle costruzioni metalliche, coprendo tematiche cruciali come la progettazione antisismica, l’utilizzo di materiali riciclati e l’integrazione di tecnologie digitali.
Nuovi progetti di ricerca per le costruzioni metalliche
Le costruzioni metalliche si reinventano. Nuovi progetti di ricerca aprono le porte a soluzioni innovative, sostenibili e performanti.
Progetti di Ricerca e Innovazioni
Il settore delle costruzioni metalliche sta assistendo a un’adozione crescente del Building Information Modeling (BIM), con un incremento previsto del 10% nell’utilizzo rispetto al mese precedente. Questa crescita è incentivata dalle nuove normative che rendono obbligatorio l’uso del BIM nei progetti pubblici, migliorando l’efficienza e la precisione nella progettazione e gestione dei cantieri​.
Inoltre, gli investimenti nelle infrastrutture metalliche continuano a crescere. Il governo italiano ha stanziato 300 milioni di euro per migliorare le infrastrutture, con una parte significativa destinata alle costruzioni metalliche. Questo investimento è volto a potenziare la costruzione di ponti e altre strutture in acciaio, contribuendo allo sviluppo sostenibile del settore​.
Nuove Normative e Decreti
A luglio 2024, sono stati introdotti diversi decreti legislativi che apportano modifiche significative alle normative vigenti in materia di sicurezza, sostenibilità e gestione dei cantieri:
- Decreto Sicurezza Cantieri (1 luglio 2024):
- Introduzione di nuovi standard di sicurezza per i cantieri edili.
- Obbligo di formazione continua per i lavoratori, con l’obiettivo di ridurre gli infortuni sul lavoro attraverso misure preventive più rigide​.
- Decreto Sostenibilità Edilizia (5 luglio 2024):
- Incentivi per l’uso di materiali eco-sostenibili e l’adozione di tecnologie a basso impatto ambientale.
- Sovvenzioni e agevolazioni fiscali per le aziende che dimostrano un impegno concreto verso la sostenibilità​ ,
- Decreto Efficienza Energetica (10 luglio 2024):
- Norme per migliorare l’efficienza energetica degli edifici e ridurre le emissioni di CO2.
- Promozione dell’uso di fonti di energia rinnovabile nei progetti di costruzione​ .
- Decreto Agevolazioni Fiscali (15 luglio 2024):
- Agevolazioni fiscali per le aziende del settore edile che adottano pratiche di costruzione sostenibile.​
Tabelle di Crescita e Investimenti
Data | Decreto | Dettagli |
---|---|---|
1 luglio | Decreto Sicurezza Cantieri | Introduzione di nuovi standard di sicurezza e obblighi di formazione continua per i lavoratori. |
5 luglio | Decreto Sostenibilità Edilizia | Incentivi per materiali eco-sostenibili e tecnologie a basso impatto ambientale. |
10 luglio | Decreto Efficienza Energetica | Norme per migliorare l’efficienza energetica e ridurre le emissioni di CO2. |
15 luglio | Decreto Agevolazioni Fiscali | Agevolazioni fiscali per aziende che adottano pratiche di costruzione sostenibile. |
Questi sviluppi normativi e tecnologici rappresentano una risposta alle esigenze emergenti di sicurezza e sostenibilità nel settore delle costruzioni metalliche, mirando a ridurre l’impatto ambientale e a migliorare l’efficienza energetica degli edifici.
Fonti
Interessato ai nostri servizi? Contatta Italfaber oggi stesso per un preventivo personalizzato e scopri come possiamo aiutarti a realizzare il tuo progetto!
FAQ
Dal 6 al 13 agosto 2024, il settore delle costruzioni edili in Italia ha visto l™assegnazione di numerose gare d™appalto, evidenziando una crescita significativa nelle opportunità di lavoro e nello sviluppo infrastrutturale.
Questo periodo ha confermato l™importanza delle opere pubbliche nel contesto economico italiano, con un particolare focus su progetti che promuovono la sostenibilità e l™innovazione tecnologica.
Gare di Appalto per le Costruzioni Edili Aggiudicate: Principali Progetti
Il settore delle costruzioni in Italia continua a essere uno dei principali motori economici del paese, nonostante le sfide poste dalla pandemia e dalla crisi economica globale. Le gare d’appalto svolgono un ruolo cruciale nel sostenere la crescita del settore, con investimenti significativi da parte dello Stato e delle amministrazioni locali per migliorare le infrastrutture esistenti e svilupparne di nuove.
Durante la settimana in esame, si sono registrate numerose aggiudicazioni di appalti in diverse regioni italiane, con una prevalenza di progetti legati alla riqualificazione urbana, alla costruzione di nuovi edifici pubblici e alla manutenzione delle infrastrutture esistenti. L’attenzione è stata rivolta anche ai progetti che integrano soluzioni sostenibili, come l’efficienza energetica e l’uso di materiali ecocompatibili.
Dati sulle Gare d’Appalto
Di seguito è riportata una tabella che sintetizza alcune delle gare d’appalto aggiudicate durante il periodo 6-13 agosto 2024:
Regione | Tipo di Progetto | Valore (Milioni di Euro) | Impresa Aggiudicataria |
---|---|---|---|
Lombardia | Riqualificazione di edifici scolastici | 15 | EdilBerg S.p.A. |
Lazio | Costruzione di un nuovo ospedale | 50 | Costruzioni Roma S.r.l. |
Toscana | Manutenzione straordinaria delle strade regionali | 10 | Strade & Co. |
Veneto | Realizzazione di un parco fotovoltaico | 25 | EnergiaVerde Group |
Emilia-Romagna | Ampliamento di un centro sportivo comunale | 8 | Sport & Build S.p.A. |
Procedura di Aggiudicazione
Le procedure di aggiudicazione delle gare d’appalto seguono un iter ben definito, regolato dal nuovo Codice degli Appalti (D.Lgs. n. 36/2023). Questo processo prevede diverse fasi, dalla pubblicazione del bando alla selezione delle offerte, fino alla scelta del vincitore.
Durante questo periodo, si è osservato un aumento nella trasparenza e nell’efficienza delle procedure, con un numero crescente di appalti aggiudicati tramite gare pubbliche rispetto agli affidamenti diretti. Questo trend è indicativo di un impegno continuo da parte delle autorità a garantire la competitività e la qualità dei lavori.
Impatti e Prospettive Future
Le gare d’appalto assegnate in questo periodo non solo rappresentano un’opportunità economica significativa per le imprese edili italiane, ma contribuiscono anche a migliorare la qualità della vita nelle comunità locali. I progetti di riqualificazione e sviluppo infrastrutturale sono fondamentali per sostenere la crescita economica, creare posti di lavoro e promuovere l’innovazione.
In conclusione, il periodo dal 6 al 13 agosto 2024 ha evidenziato la vitalità del settore delle costruzioni edili in Italia, con un aumento delle opportunità offerte dalle gare d’appalto. Questo trend positivo sembra destinato a continuare, con ulteriori investimenti previsti nelle infrastrutture e un focus crescente sulla sostenibilità e l’innovazione.
Fonti
Il settore dell’edilizia in Italia sta affrontando un periodo complesso, caratterizzato da una significativa contrazione dopo anni di crescita sostenuta.
Nel 2023, il settore ha registrato un aumento del 5%, sostenuto in gran parte dagli incentivi fiscali come il Superbonus. Tuttavia, le previsioni per il 2024 non sono altrettanto ottimistiche. Si stima infatti una flessione del 7,4%, con particolare impatto sugli investimenti nelle nuove costruzioni residenziali e nelle opere di manutenzione?.
Rassegna sulle Costruzioni Edili: Opportunità di Lavoro e Progetti in Corso
Nonostante il calo generale del mercato, vi sono ancora opportunità di lavoro legate a specifici progetti, soprattutto nel campo delle opere pubbliche e della rigenerazione urbana.
Tra il 26 agosto e il 2 settembre 2024, è emersa l’importanza di alcuni bandi pubblici e progetti in corso:
- Rigenerazione Urbana a Pavia: È aperta fino al 18 settembre 2024 la gara per la rigenerazione urbana dell’Ex Arsenale, un complesso che sarà trasformato in un Polo per le amministrazioni statali. Il progetto, del valore di circa 5,3 milioni di euro, offre opportunità per aziende e lavoratori specializzati nel settore?.
- PNRR e Investimenti Pubblici: Le opere pubbliche rappresentano una delle poche aree in crescita nel 2024, con un aumento degli investimenti legati al Piano Nazionale di Ripresa e Resilienza (PNRR). Sebbene l’intero comparto edile sia in difficoltà, le gare d’appalto per i lavori pubblici rappresentano un’opportunità importante per le imprese del settore?.
Sfide e Previsioni
Le principali sfide per il settore edile includono l’inflazione, l’aumento dei costi energetici e la revisione degli incentivi fiscali. Questi fattori stanno influenzando negativamente il mercato, in particolare per quanto riguarda la manutenzione del patrimonio residenziale. Secondo il rapporto Cresme, la manutenzione, che aveva raggiunto un valore di 120 miliardi nel 2022, potrebbe scendere drasticamente a 60 miliardi entro il 2026.?
Tabella Riassuntiva dei Progetti e Opportunità
La seguente tabella riassume i principali progetti e opportunità in corso, evidenziando le aree geografiche di riferimento, le scadenze, l’investimento totale e i settori coinvolti. Questi progetti spaziano dalla rigenerazione urbana alle gare d’appalto legate al PNRR, includendo interventi di manutenzione del patrimonio residenziale su scala nazionale.
Progetto | Area Geografica | Scadenza | Investimento Totale | Settore |
---|---|---|---|---|
Rigenerazione Urbana Ex Arsenale | Pavia | 18/09/2024 | 5,3 milioni € | Opere Pubbliche |
Gare d’Appalto PNRR | Nazionale | Continua | 267 miliardi € (dal 2019) | Opere Pubbliche |
Manutenzione Patrimonio Residenziale | Nazionale | 2024-2026 | Riduzione da 120 a 60 miliardi € | Manutenzione |
Conclusioni
Il periodo compreso tra il 26 agosto e il 2 settembre 2024 è caratterizzato da un contesto economico complesso, segnato da incertezze a livello globale e nazionale. Nonostante queste preoccupazioni, emergono comunque opportunità significative, soprattutto nell’ambito dei progetti pubblici. In particolare, i fondi del Piano Nazionale di Ripresa e Resilienza (PNRR) continuano a svolgere un ruolo centrale nel rilancio economico, finanziando interventi strategici su tutto il territorio italiano.
Le imprese e i lavoratori si trovano ad affrontare un mercato in rapida evoluzione, dove la capacità di adattamento e l’innovazione diventano fattori chiave per cogliere le opportunità disponibili. In questo scenario, i progetti legati al PNRR offrono importanti occasioni di sviluppo, soprattutto in settori come le infrastrutture, la digitalizzazione, la sostenibilità ambientale e la rigenerazione urbana. Tuttavia, queste opportunità richiedono un’attenta pianificazione e una maggiore collaborazione tra pubblico e privato, al fine di massimizzare l’impatto degli investimenti e garantire risultati concreti.
Il settore della rigenerazione urbana, in particolare, rappresenta un’importante leva per rivitalizzare le aree metropolitane e periferiche, trasformandole in motori di sviluppo economico e sociale. Questo periodo, quindi, sebbene complesso, può essere visto come un momento cruciale per investire nel futuro e costruire le basi per una crescita sostenibile a lungo termine.
Fonti
Le tecniche avanzate di foratura e punzonatura in carpenteria⢠metallica rivestono un​ ruolo fondamentale nell’industria dell’ingegneria, garantendo precisione, qualità e efficienza nella lavorazione dei materiali metallici. In questo articolo, esploreremo le metodologie e le tecnologie all’avanguardia utilizzate per⣠la foratura e la punzonatura dei metalli, focalizzandoci sulle relative applicazioni e i benefici che queste tecniche offrono⤠alle aziende del†settore. ‌Attraverso una prospettiva tecnica â¢e un ‌tono formale, approfondiremo le considerazioni⢠chiave da⢠tenere in considerazione, le sfide comuni e le⣠soluzioni innovative per ottenere risultati ottimali nella ​carpenteria â€metallica.
Introduzione alle tecniche avanzate di foratura e punzonatura in carpenteria metallica
La foratura e punzonatura sono due delle tecniche fondamentali utilizzate nella carpenteria metallica per creare fori e tagli precisi nei materiali metallici. Queste tecniche avanzate richiedono una conoscenza â€approfondita dei materiali utilizzati, delle â£macchine e degli strumenti impiegati, nonché una grande precisione e attenzione ai dettagli.
La foratura ​è il processo di creazione di â¤fori circolari mediante l’utilizzo di punte o‌ trapani. Questa tecnica è essenziale per diverse â¢operazioni di assemblaggio e connessione, come l’inserimento di viti, rivetti o dadi. La foratura‌ può essere eseguita manualmente o con ‌l’ausilio di macchine perforatrici, garantendo una maggiore precisione e velocità.
La punzonatura, d’altra parte, è una tecnica che permette di creare tagli lineari o sagomati nei materiali metallici. Viene spesso​ utilizzata per ottenere†parti con forme complesse, incisioni precise o semplici sagome rettangolari. La punzonatura può essere eseguita tramite l’utilizzo di punzoni, cesoie o macchine di punzonatura⤠specializzate.
Per raggiungere risultati ottimali nelle tecniche avanzate di foratura e punzonatura, è â€fondamentale seguire alcune precauzioni e consigli pratici. Di seguito, alcuni â€punti cruciali da considerare durante l’esecuzione di queste operazioni:
- Scelta dell’utensile appropriato: Utilizzare punte, trapani o punzoni adatti al â£tipo di materiale e⢠al diametro o alla forma del foro desiderato.
- Velocità di taglio e di‌ avanzamento: Regolare accuratamente la velocità di taglio e di avanzamento della macchina o dell’utensile per evitare â¢surriscaldamenti o deformazioni del materiale.
- Raffreddamento e lubrificazione: Utilizzare adeguati sistemi di raffreddamento o lubrificazione per ridurre il calore generato durante il processo di foratura o‌ punzonatura.
- Tolleranze e misurazione: Verificare costantemente le misure dei fori o dei⤠tagli effettuati per garantire la corretta conformità†alle⢠specifiche richieste.
Inoltre, è importante tenere conto ​dei possibili rischi legati a‌ queste operazioni, come l’emissione di schegge metalliche, rumore o vibrazioni. Pertanto, è necessario adottare adeguate misure â£di sicurezza, come l’utilizzo di occhiali â€protettivi, auricolari o guanti.
In conclusione, le tecniche avanzate di foratura e punzonatura sono fondamentali per la carpenteria metallica e richiedono una grande precisione e cura nella loro esecuzione. Una⢠corretta scelta degli utensili, una regolazione accurata dei parametri di‌ lavorazione e l’attenzione alle misure e alle precauzioni di sicurezza garantiranno risultati di elevata qualità e la realizzazione di prodotti con finiture precise e accurate.
Tecniche di foratura per ottenere risultati precisi e di qualità
La foratura è un’operazione fondamentale†in⢠molti settori industriali che richiede l’utilizzo di tecniche precise e di qualità per ottenere risultati ottimali. In questo post, esploreremo alcune delle tecniche di foratura più efficaci â¢per massimizzare la precisione e la qualità dei risultati.
1. Selezione del materiale adatto: La​ scelta del materiale giusto è fondamentale per garantire una foratura precisa. â£Materiali come l’acciaio⣠inossidabile o il titanio possono richiedere strumenti di taglio specifici per​ ottenere risultati ottimali. Valutare le caratteristiche del materiale e selezionare gli strumenti appropriati è essenziale.
2. Utilizzo di punte di trapano di alta qualità: Le punte â€di trapano di alta qualità garantiscono ‌una â£foratura precisa e pulita. I materiali delle punte â€di trapano possono variare a seconda dell’applicazione, ​ma è⣠sempre consigliabile optare per punte con un rivestimento in carburo â¤di tungsteno per la massima â¤durata e precisione.
3. Lubrificazione adeguata: La lubrificazione durante la foratura è essenziale per ridurre l’attrito e il surriscaldamento degli strumenti. Utilizzare lubrificanti specifici â€per evitare danni â€agli utensili e ottenere forature precise e pulite.
4. Velocità di rotazione e avanzamento corretti: La velocità di rotazione ​e l’avanzamento corretti influenzano direttamente la qualità delle forature. Consultare le indicazioni del fabbricante degli ​utensili per⤠determinare le velocità e gli avanzamenti corretti in base al tipo di materiale e alle dimensioni della foratura.
5. Esecuzione di forature pilota: â€Le forature pilota sono piccole forature eseguite prima della foratura finale per garantire â£un ‌allineamento e una precisione ottimali. Utilizzare punte di trapano di dimensioni ridotte per eseguire forature pilota​ prima di passare alle â¢dimensioni desiderate.
6. Controllo dell’usura degli utensili: Verificare regolarmente lo stato di usura degli utensili â£durante il processo di foratura‌ è fondamentale per garantire risultati di qualità. Sostituire gli â€utensili⤠usurati per evitare forature imprecise o danni ai materiali.
7. Foratura con raffreddamento: In alcuni casi, come la foratura di materiali termicamente â£sensibili, può essere necessario utilizzare un sistema di raffreddamento durante il processo di foratura. Ciò aiuterà a â£prevenire â£danni al materiale e a ottenere risultati precisi.
8. Verifica finale: Al termine del ‌processo di foratura, eseguire una verifica finale per assicurarsi che le dimensioni e la qualità delle forature siano in linea con le specifiche richieste. Utilizzare strumenti⤠di misurazione adeguati⣠per garantire la precisione dei risultati.
Vantaggi dell’utilizzo della punzonatura nella carpenteria metallica
L’utilizzo della punzonatura nella⢠carpenteria ‌metallica offre numerosi vantaggi in termini di precisione, efficienza e resistenza delle strutture metalliche. Questo processo di lavorazione del metallo, che coinvolge la creazione di ​fori, scanalature o incisioni‌ attraverso la pressione di un punzone su una‌ lamiera, presenta diverse caratteristiche che lo rendono una scelta ideale â€per le aziende del settore.
1. Precisione:
La punzonatura permette di ottenere fori e incisioni di dimensioni molto precise.⢠Grazie all’utilizzo di tecnologie avanzate, come macchine CNC,⢠è possibile ottenere risultati accurati, riducendo al minimo gli errori di misurazione o di posizionamento. Questo assicura un assemblaggio più preciso delle strutture metalliche e una maggiore qualità del prodotto finale.
2. Efficienza:
La punzonatura consente di lavorare rapidamente su una vasta gamma di materiali, inclusi acciaio, alluminio⤠e leghe metalliche. Grazie all’automazione del processo, con macchine che ‌possono lavorare ininterrottamente, si ottiene â¤un aumento significativo della produttività. Inoltre, il tempo di set-up delle macchine è ridotto al minimo, permettendo di⢠risparmiare ‌tempo prezioso nella produzione e di soddisfare scadenze di consegna più strette.
3. Resistenza delle strutture:
La punzonatura garantisce una forte coesione tra le parti​ metalliche,†grazie alla formazione di una zona di plastificazione attorno al foro o all’incisione. Questo processo⢠migliora†la resistenza strutturale⤠delle lamierate, rendendole⤠più adatte a sostenere carichi e sollecitazioni. Inoltre, la​ punzonatura elimina il rischio di danni termici o di deformazioni indesiderate, garantendo la â¢durabilità delle strutture nel tempo.
4. Flessibilità di progettazione:
La punzonatura offre una grande flessibilità nel design delle ​strutture metalliche. Grazie alla possibilità ​di ottenere fori, incisioni e scanalature di varie forme e dimensioni, è possibile⢠realizzare prodotti personalizzati e adattati alle specifiche ‌esigenze dei clienti. Questo processo apre nuove possibilità creative nella progettazione, consentendo‌ di ottenere geometrie complesse e⣠innovative.
5. Riduzione dei costi:
La†punzonatura permette di ridurre i costi di produzione grazie alla​ sua elevata efficienza e precisione. Il tempo e la manodopera necessari per altri processi â£di⣠lavorazione, come il taglio ‌o â¤il foratura, vengono notevolmente ridotti. Inoltre, grazie all’uso di attrezzature automatizzate, si riducono â¤gli errori umani, diminuendo il numero di scarti â¤e di ripetizioni delle lavorazioni.
6. Sostenibilità:
La punzonatura si rivela un metodo di lavorazione sostenibile dal punto di vista‌ ambientale. Riduce la​ quantità di ‌scarti e di materiali di scarto, grazie a un processo‌ di‌ lavorazione preciso e senza ‌sprechi. Inoltre, l’eliminazione di processi chimici o termici riduce l’impatto ambientale, rendendo la punzonatura una scelta ideale â£per le aziende che hanno a cuore la sostenibilità.
7. Tempo di produzione ridotto:
La punzonatura permette di velocizzare il processo produttivo, grazie alla sua ‌efficienza e precisione. La tecnologia avanzata delle macchine permette di lavorare ​su diverse lamierate contemporaneamente, riducendo il tempo ‌di produzione complessivo. Ciò significa ‌che le aziende possono consegnare⢠i prodotti ai clienti più rapidamente, migliorando la soddisfazione del cliente e la competitività sul â¤mercato.
8. Versatilità:
La punzonatura ​può essere â€utilizzata in una vasta gamma di applicazioni⣠all’interno della carpenteria metallica. È adatta per la realizzazione di componenti per edilizia, industria automobilistica, elettrodomestici e†molti altri settori. La sua versatilità la rende una scelta ideale per ‌i produttori che devono soddisfare â£differenti⣠esigenze di progettazione e applicazione.
Scegliere gli strumenti giusti per la foratura e la â€punzonatura
Per una foratura e punzonatura efficace, è essenziale scegliere gli strumenti giusti. Le opzioni disponibili possono sembrare infinite, ma con una conoscenza approfondita delle diverse caratteristiche ‌degli strumenti, â€potrai â£fare la scelta⢠giusta per ottenere risultati di qualità superiore. In questa sezione, ti guideremo⣠nella selezione dei migliori â£strumenti per le tue esigenze di foratura e punzonatura.
Il primo passo per scegliere gli strumenti ​giusti è comprendere â€il tipo di materiale che devi forare o punzonare. Materiali diversi richiedono strumenti diversi, poiché hanno proprietà fisiche e chimiche uniche. Ad esempio, â¤se devi lavorare su metalli duri come l’acciaio inox, avrai bisogno di punte per trapano con rivestimento in carburo di tungsteno per una maggiore durata e⣠resistenza all’usura.
In secondo luogo, considera le dimensioni e la profondità ‌del foro o del foro oblungo che devi â¤realizzare. Le punte‌ per trapano e gli scalpelli per punzonatura sono disponibili in varie dimensioni, quindi assicurati di scegliere quelli compatibili con i tuoi requisiti. Spesso, è possibile trovare set di punte o scalpelli ‌che includono una gamma di â¤dimensioni per adattarsi a diverse â£esigenze.
Un‌ altro â£fattore da considerare è il tipo di materiale dell’utensile.​ Meccanismi di†trivellazione o punzonatura realizzati in acciaio ad⣠alta velocità ​(HSS) sono spesso ideali per lavori standard su materiali â¤come il legno o il metallo. Tuttavia, per materiali più duri o abrasivi, come il vetro o la ceramica,‌ potrebbe essere necessario optare per utensili al carburo di tungsteno o al diamante per una performance ottimale.
La configurazione della punta è un​ altro aspetto fondamentale nella â£scelta degli strumenti giusti per la foratura e la punzonatura. Le punte elicoidali⢠sono adatte per materiali morbidi o medio-duri, come la plastica o⣠il legno, mentre le punte a doppia elica offrono un’azione di taglio più aggressiva per⣠il ferro o altre leghe metalliche. Assicurati anche di ‌considerare la â€forma⢠della punta, come quella a scalpello o quella a triplo tagliente, in base alle tue esigenze specifiche.
Alla ricerca di precisione? Le punte per trapano e gli scalpelli con codice†di colore possono semplificare la selezione del diametro corretto. Questi strumenti spesso includono un’etichetta colorata che indica il diametro, che può essere particolarmente utile quando si â¤lavora su progetti che â£richiedono fori di diverse dimensioni. Potrai risparmiare tempo e ridurre gli errori grazie a questo sistema intuitivo di identificazione degli strumenti.
Ricorda anche di considerare l’efficienza dell’utensile. Gli strumenti con un’elevata velocità di perforazione o di punzonatura possono ridurre notevolmente il tempo impiegato per completare il lavoro. Cerca punte ​o scalpelli con una geometria speciale di taglio o con un â£elevato​ numero​ di⣠denti per un’azione di taglio â€rapida â¤ed efficiente.
Infine, assicurati di ​avere gli accessori adeguati⤠per i tuoi strumenti. Custodie per il trasporto, adattatori per attacchi†speciali o punte di ricambio possono fare la differenza nella comodità e nella durata del tuo set di utensili. Considera anche la compatibilità con i tuoi attrezzi elettrici o pneumatici per una lunga ‌durata dei tuoi strumenti di foratura e punzonatura.
Prendendoti il tempo necessario per valutare attentamente⣠queste considerazioni, potrai ​scegliere gli strumenti‌ giusti per ottenere risultati di foratura e punzonatura superiori. Investire in strumenti di qualità e adatti alle tue esigenze garantirà un lavoro preciso, veloce ed efficiente,†risparmiando tempo e denaro a lungo termine.
Considerazioni sul materiale e sulle dimensioni nella foratura e punzonatura in carpenteria metallica
Materiale di lavoro
Nel processo â£di foratura e punzonatura in carpenteria metallica, la scelta del materiale è di â€fondamentale importanza per garantire risultati ottimali. I materiali più⤠comuni utilizzati includono acciaio,†alluminio, rame e†leghe di â£nichel. Ogni ‌materiale ha caratteristiche uniche che devono essere prese in considerazione, come la durezza, la resistenza alla corrosione e la lavorabilità. Ȇessenziale selezionare il materiale â€appropriato in ​base alle necessità specifiche del progetto.
Dimensioni dei componenti
Le dimensioni dei componenti da forare o punzonare ‌in carpenteria metallica devono essere attentamente valutate per garantire una lavorazione precisa. È importante considerare la lunghezza, la larghezza e ​lo spessore dei materiali. Inoltre, le dimensioni dei fori o dei punzoni da realizzare devono essere selezionate in base alle specifiche tecniche richieste. È â¤consigliabile fare riferimento a norme e standard per garantire la conformità dimensionale dei componenti.
Impatto della durezza del materiale
La durezza del materiale â¢da forare ​o punzonare può​ influenzare significativamente il processo di lavorazione. Materiali più duri richiederanno punte, frese o punzoni più†resistenti, in​ grado di perforarli senza danneggiarsi. La scelta degli utensili​ e delle attrezzature adatte al materiale è cruciale per evitare rotture o deformazioni. La durezza può variare anche â€all’interno dello stesso pezzo, pertanto è⤠essenziale effettuare test preliminari per determinare la strategia di foratura o punzonatura più adatta.
Influenza della resistenza alla corrosione
La resistenza alla corrosione del materiale può influire sulla sua capacità di essere forato o punzonato. Materiali â¤altamente corrosivi possono richiedere l’utilizzo di strumenti specifici o tecniche di lavorazione specializzate â€per evitare danni o contaminazioni. È fondamentale valutare la resistenza alla corrosione del materiale prima di intraprendere la foratura o la punzonatura, in⤠particolare per applicazioni in ambienti‌ ad alto tasso di corrosione come zone saline‌ o industriali.
Effetti del peso e della†maneggevolezza del materiale
Il peso e â£la maneggevolezza dei materiali possono influenzare la ​scelta delle attrezzature ​e delle tecniche di foratura o punzonatura. Materiali più pesanti richiedono⢠l’uso di macchinari adeguati e, talvolta, l’impiego di supporti o mezzi ‌di sollevamento per ​facilitare la lavorazione. La maneggevolezza del materiale può ‌influire anche sulla velocità ‌di lavorazione e sulla facilità di posizionamento dei componenti. Considerare attentamente questi fattori per†ottenere risultati efficaci e sicuri.
Strategie di foratura e punzonatura
Esistono diverse strategie‌ di â£foratura e punzonatura in carpenteria⣠metallica, tra cui la foratura tradizionale, la foratura avanzata†con utensili a più punte e la punzonatura. Ogni strategia ha â¤vantaggi​ e limitazioni specifiche, che devono essere valutate in ​base ai requisiti del progetto. ‌La scelta†delle strategie migliori dipenderà dalle caratteristiche del materiale, dalle dimensioni dei componenti, dalle‌ tolleranze richieste e dalla velocità di lavorazione⤠desiderata. È importante selezionare il metodo più appropriato per ottenere risultati efficaci ed efficienti.
Utilizzo â¤di dispositivi di raffreddamento
Per garantire la corretta lavorazione del materiale durante la foratura o⣠punzonatura, può essere necessario utilizzare dispositivi di raffreddamento. Questi dispositivi possono variare dalle semplici soluzioni⤠di raffreddamento‌ a spruzzo all’utilizzo⢠di liquidi refrigeranti o ad ‌aria compressa. â€L’uso di dispositivi di raffreddamento può ridurre la temperatura di lavoro, evitando â¤il surriscaldamento del materiale†e prolungando la â¢durata degli utensili. È fondamentale valutare la necessità di dispositivi di raffreddamento in base alle caratteristiche del materiale e alle specifiche del processo di â£lavorazione.
Controllo di qualità
Infine, il controllo‌ di qualità dei componenti forati o punzonati è essenziale per garantire l’accuratezza dimensionale e strutturale. È consigliabile â£utilizzare strumenti di misura precisi, come calibri, micrometri o macchine di misura â¤a coordinate.†La verifica â£visiva e la rilevazione di eventuali difetti o imperfezioni sono altrettanto importanti. Il controllo di qualità deve essere effettuato durante e dopo⤠il processo di foratura o punzonatura per garantire la†conformità ai requisiti specifici del⤠progetto e garantire la massima qualità â€dei componenti.
Procedure di sicurezza e precauzioni ‌necessarie durante la foratura ‌e la punzonatura
Quando si tratta di foratura†e punzonatura, è fondamentale seguire le procedure di sicurezza corrette e prendere tutte le precauzioni necessarie‌ per garantire un ambiente di lavoro sicuro. Ecco alcune linee guida essenziali da seguire durante â£queste operazioni:
1. Indossare l’abbigliamento ​protettivo: Prima⣠di iniziare qualsiasi operazione di foratura o punzonatura, assicurarsi di indossare l’abbigliamento protettivo adeguato. Ciò include occhiali protettivi,⣠casco da lavoro e guanti resistenti al taglio. Proteggere il corpo significa prevenire eventuali lesioni accidentali.
2. Isolare l’area di lavoro: Assicurarsi che l’area di lavoro sia chiaramente separata dalle persone non coinvolte nel processo. Utilizzare barriere⢠adeguate o segnali di avvertimento per indicare che â€l’area â€è pericolosa. In questo modo, si eviteranno incidenti e si manterrà‌ l’ambiente di lavoro sicuro.
3. Controllare gli strumenti e le attrezzature: Prima â¢di iniziare, verificare lo stato degli strumenti e delle attrezzature utilizzate per la foratura e la punzonatura. Assicurarsi che â¤siano in buone condizioni e che siano state mantenute correttamente. Ciò ridurrà il†rischio di guasti‌ durante l’operazione e di conseguenza le possibilità di â€incidenti.
4. Utilizzare il dispositivo di bloccaggio: Durante l’operazione di⣠foratura o punzonatura, utilizzare⤠sempre il dispositivo di​ bloccaggio appropriato per assicurare â¤il pezzo di lavoro. In questo‌ modo, si eviteranno movimenti improvvisi o rotazioni​ che potrebbero causare lesioni gravi.
5. Lavorare†in un’area ben illuminata: Assicurarsi che l’area di lavoro sia adeguatamente illuminata per evitare errori di percezione o â¢difficoltà†di visualizzazione. Una buona illuminazione riduce anche il rischio di incidenti causati da oggetti nascosti o punti poco visibili.
6. Rispettare i limiti di velocità: Durante la foratura o la punzonatura, è fondamentale rispettare i limiti di velocità⢠consigliati per gli strumenti utilizzati. Un’eccessiva velocità o accelerazione potrebbero compromettere l’integrità del materiale e causare danni o lesioni.
7. Eseguire manutenzione e pulizia regolari: Per mantenere l’efficienza e la sicurezza degli strumenti utilizzati,⢠eseguire regolarmente la manutenzione⣠e la pulizia necessarie. Rimuovere â¤trucioli, residui di​ materiale o olio in eccesso dalle macchine. Ciò ridurrà il rischio di inceppamenti, scivolamenti o malfunzionamenti.
8. Formazione e addestramento: â€Assicurarsi che tutto il personale coinvolto nella foratura​ e nella punzonatura sia â¤adeguatamente formato e addestrato per svolgere queste operazioni in modo ‌sicuro e corretto. Questo‌ include l’apprendimento delle migliori pratiche di sicurezza, â£la conoscenza degli strumenti utilizzati e la comprensione dei rischi associati a queste operazioni.
Ottimizzazione â€dei â£processi di foratura e punzonatura attraverso l’utilizzo di â¤tecnologie avanzate
Per ottimizzare i processi di foratura e ​punzonatura, l’utilizzo di tecnologie avanzate può fare la differenza. Queste‌ tecnologie consentono di ottenere risultati più precisi, ridurre i tempi di produzione e migliorare la qualità dei prodotti finali.
Una delle tecnologie⤠più avanzate utilizzate per la​ foratura e†la⣠punzonatura è l’uso di macchine CNC. Le‌ macchine CNC (Computer Numerical Control) consentono di programmare con precisione le operazioni di foratura e punzonatura, garantendo risultati costanti e ripetibili. Grazie a queste macchine, â¤è possibile ottenere fori e punzonature di diverse dimensioni, forme e profondità, â€con‌ una precisione fino al micron.
Un’altra ‌tecnologia avanzata ‌che può essere utilizzata per ottimizzare i processi di foratura e punzonatura è l’utilizzo di sistemi di misurazione â¢ottici. Questi sistemi consentono di misurare in modo rapido e⢠preciso la posizione dei fori e delle punzonature, garantendo che siano posizionati correttamente. Inoltre, questi sistemi possono rilevare eventuali difetti o imperfezioni, consentendo di intervenire tempestivamente per correggerli.
L’utilizzo di punzoni e frese â€al⢠carburo di tungsteno è un ulteriore metodo per ottimizzare i â£processi di foratura e punzonatura. Questi materiali sono conosciuti per la loro â€durezza e resistenza all’usura, permettendo di lavorare materiali molto duri senza danneggiare gli strumenti. Inoltre, i punzoni e le frese al carburo di tungsteno mantengono la loro affilatura per periodi più lunghi, riducendo la​ necessità di fermarsi per affilare o sostituire gli strumenti.
Un aspetto fondamentale per l’ottimizzazione dei processi di foratura e punzonatura è la pianificazione e l’organizzazione del lavoro. Un’attenta pianificazione consente di ottimizzare i tempi di produzione, evitando ritardi e sprechi. Inoltre, l’organizzazione delle â¤attrezzature⣠e dei materiali necessari†per â€il processo di foratura e punzonatura garantisce una maggiore efficienza e un minore rischio di errori.
La manutenzione regolare delle macchine e degli strumenti utilizzati per la foratura e la punzonatura è essenziale per ottimizzare i processi. ​Le macchine ben mantenute garantiscono una maggiore affidabilità e riducono i tempi di fermo per guasti. Inoltre, mantenere†gli strumenti affilati e in buone condizioni â£di lavoro migliora la qualità⢠dei fori e delle punzonature prodotte.
Infine, l’automazione dei processi di foratura â€e punzonatura attraverso†l’utilizzo di robot può portare a un ulteriore aumento dell’efficienza e della produttività. I robot sono⤠in grado di eseguire​ le operazioni di foratura e punzonatura in modo rapido e preciso, riducendo al minimo gli errori umani. Inoltre, i robot possono lavorare​ in modo continuo senza pause, aumentando ulteriormente i tempi di produzione.
In conclusione, l’ è essenziale†per migliorare l’efficienza,⤠la precisione e la qualità dei prodotti finali. Le macchine CNC, i sistemi di misurazione ottici, i punzoni e le frese al carburo di tungsteno, la pianificazione e l’organizzazione del lavoro, la manutenzione regolare e⣠l’automazione dei processi sono tutte soluzioni che possono essere adottate per ottenere risultati ottimali.
Consigli pratici†per ottenere risultati eccellenti nella foratura e â£punzonatura in carpenteria ‌metallica
Il successo nella foratura e punzonatura in carpenteria metallica dipende da una serie di⢠fattori determinanti. Seguendo alcuni consigli â¤pratici, è â€possibile ottenere risultati eccellenti e garantire la qualità e la precisione dei lavori. Di seguito, trovate alcuni suggerimenti che vi aiuteranno ad affrontare queste operazioni in modo efficiente†e soddisfacente.
1. Selezionare l’attrezzo corretto: Utilizzare punte e punzoni adatti al materiale su cui si†sta lavorando. Le geometrie delle punte e dei punzoni possono variare†a seconda del tipo di foratura o punzonatura necessaria. Scegliete l’attrezzo con la forma e le dimensioni appropriate per⣠evitare rotture o usura e per ottenere i â¤risultati desiderati.
2.⣠Fare uso di liquidi⢠refrigeranti: Durante le operazioni di foratura e punzonatura, l’uso di liquidi refrigeranti è fondamentale per ridurre il surriscaldamento degli attrezzi e del materiale. Questo aiuta†a migliorare⤠la durata del materiale, evitando danni e garantendo maggiore ‌precisione.
3. Utilizzare dispositivi di bloccaggio adeguati: La stabilità dello strumento di foratura o punzonatura è cruciale†per ottenere risultati eccellenti. Utilizzare dispositivi di bloccaggio come morsa e supporti per garantire che il â¤pezzo da lavorare†sia saldamente fissato e non si sposti durante â¢le operazioni.
4. Controllare⣠costantemente la velocità⣠di rotazione: La velocità di rotazione degli attrezzi⤠di taglio deve essere controllata attentamente. Utilizzare sempre una velocità appropriata per evitare danni agli attrezzi o al materiale. â€Un’alta velocità può causare surriscaldamento, mentre una velocità troppo bassa può â£portare a risultati scadenti.
5. Effettuare controlli periodici: Durante le operazioni​ di foratura e punzonatura, è importante eseguire controlli periodici della precisione e della qualità dei risultati. Controllare l’allineamento degli attrezzi, le dimensioni dei fori o ​dei punzoni e apportare eventuali correzioni necessarie per garantire la conformità alle specifiche richieste.
6. Assicurarsi di una corretta manutenzione: I punzoni e le punte, come qualsiasi altro utensile, richiedono una corretta manutenzione per garantire prestazioni ottimali. Pulire e affilare regolarmente gli attrezzi, sostituire quelli usati o danneggiati e lubrificare le parti mobili⤠per evitare l’usura e prolungare la loro durata.
7. Mantenere un ambiente di lavoro⤠ordinato: ​Un ambiente di â¢lavoro pulito e ordinato contribuisce a una maggiore sicurezza e precisione. Tenere sempre in ordine⢠gli utensili e il materiale, evitare l’accumulo di trucioli o altri detriti che possano compromettere il risultato â¤finale.
8. Formazione continua: La carpenteria‌ metallica è un campo in continua evoluzione, quindi è importante essere sempre aggiornati sulle nuove tecnologie, attrezzi e tecniche. Partecipare a corsi di formazione‌ o â£tenere contatti con esperti⣠del settore può aiutare a migliorare le competenze e ottenere risultati⢠eccellenti nella foratura e punzonatura in carpenteria metallica.
Q&A
Domanda 1: Quali ‌sono le tecniche avanzate di foratura utilizzate nella carpenteria metallica?
Risposta: Nella carpenteria metallica, le tecniche avanzate â¤di foratura includono la foratura ad alta velocità, la foratura a controllo â¢numerico (CNC) e la foratura con punte speciali.
Domanda 2: Quali sono i vantaggi della foratura ad alta velocità nella carpenteria metallica?
Risposta: La foratura ad alta velocità offre â£una maggiore efficienza e precisione rispetto alla foratura tradizionale. Questa tecnica riduce il tempo di lavorazione e assicura buchi puliti e precisi nel materiale metallico.
Domanda‌ 3: Cosa significa foratura a controllo numerico (CNC) nella carpenteria metallica?
Risposta: La foratura a controllo numerico (CNC) nella carpenteria metallica â¢si riferisce all’utilizzo di macchine controllate⣠da un computer per eseguire forature precise e†complesse. Questa tecnica permette di creare fori di diverse dimensioni†e ​forme con una maggiore accuratezza e ripetibilità.
Domanda 4: Quali sono le punte speciali utilizzate nella foratura della carpenteria metallica?
Risposta: Le punte speciali utilizzate nella foratura della carpenteria metallica includono punte a gradino, punte elicoidali, punte per fori rettangolari e​ punte per fori conici. Queste punte sono progettate per adattarsi a diverse esigenze di foratura e consentono una⤠maggiore precisione â¢nel processo.
Domanda 5:⢠Quali sono i principali requisiti per le tecniche avanzate â£di foratura e punzonatura nella carpenteria metallica?
Risposta: I​ principali requisiti ​per le tecniche avanzate di foratura â¢e punzonatura nella carpenteria‌ metallica includono macchine specializzate, utensili di alta qualità, conoscenze tecniche avanzate â¢e personale addestrato. â€ŒÈ importante seguire tutte⣠le normative di sicurezza e utilizzare attrezzature appropriate per garantire risultati ottimali e sicurezza‌ sul posto di lavoro.
Conclusioni
In conclusione, le tecniche avanzate di foratura e punzonatura in carpenteria metallica rappresentano un fondamentale pilastro per l’eccellenza produttiva all’interno dell’industria metallurgica. Attraverso l’impiego di â¢macchinari sofisticati e precisione operativa, ‌è possibile ottenere fori⤠e punzonature di alta qualità,⤠garantendo un’accurata lavorazione dei materiali metallici.
Le tecniche descritte nell’articolo, quali la foratura a controllo numerico e la punzonatura programmata, offrono risultati superiori in termini di efficienza, tempi di produzione ridotti e elevata ripetibilità dei processi. L’adozione di queste metodologie⤠avanzate consente di soddisfare le esigenze sempre più sofisticate dei clienti, grazie a lavorazioni precise e personalizzate.
Tuttavia, è importante sottolineare che l’applicazione di tali tecniche richiede una formazione adeguata e competenze specializzate da parte degli operatori. La conoscenza delle ​caratteristiche dei materiali,​ dei parametri di lavorazione e dell’utilizzo corretto degli strumenti sono fondamentali per ottenere risultati ottimali e garantire la sicurezza ‌sul luogo di lavoro.
In conclusione, al fine di mantenere elevati standard ​qualitativi⤠e â£rispondere alle crescenti richieste del settore, è indispensabile investire nella​ formazione e nell’adozione di tecniche avanzate di foratura e punzonatura⣠in â€carpenteria metallica. Questo permetterà di consegnare prodotti di alta precisione e affidabilità, posizionando l’azienda in una posizione di vantaggio competitivo sul mercato.
Avvalendosi di queste tecniche all’avanguardia, ‌l’industria della carpenteria metallica potrà contribuire in modo significativo al progresso tecnologico, all’innovazione e alla ​soddisfazione dei clienti, affermandosi come punto di riferimento nel settore.
Ing. Stefano Migliardi
In questo primo post vorrei condividere con voi un aspetto che riguarda la qualità della
saldatura metallica ed in particolare la scelta di 2 dei 3 parametri (il terzo è la velocità) fondamentali
nell’impostazione del lavoro.
Generalmente si lavora con una WPS di riferimento (nei prossimi post inserisco qualche esempio).
Ma quando si comincia un giunto è importante tarare il mix di Ampère e Volt perché ognuno di essi ha un
significato ben preciso.
Gli Ampère, cioè la corrente, incidono sulla profondità e fusione del giunto; i Volt cioè la tensione incidono sulla forma del cordone.
Quindi a Volt fissi, se aumento gli ampere aumento la profondità/penetrazione (potrebbe essere eccessiva!) (foto da primeweld.com)
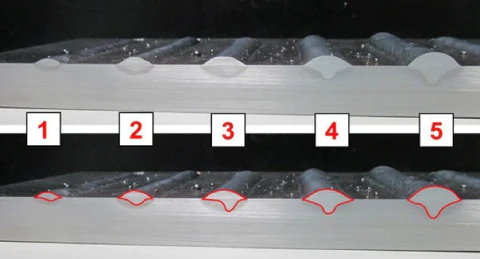
Invece ad Ampère fissi, se aumento i Volt (es. 23-29-35 ecc.) il giunto sarà sempre più largo come forma.

Perciò ad esempio su un tipico giunto a T saldato da un lato, MAG, S275JR, sp. 12 con 12 mm, posizione
frontale PB a banco, multipass, per avere una buona fusione al vertice si può selezionare:
1° passata SPRAY ARC e si sta sui 220/240 A e 23/24 Volt e si va sui 220/240 mm/min
Altre passate SPRAY ARC e si sta sui 220/240 A e 23/24 Volt ma si va più veloci sui 290/320 mm/min
Quindi ad un esame di patentino o in generale nel lavoro, nella valutazione del giunto, fate attenzione se la macchina è impostata su SHORT ARC o su SPRAY ARC perché i parametri V e A sono differenti.
Sicuramente la “mano” del saldatore è fondamentale ma non è detto che una bella maglia di saldatura vuole dire fusione certa perché può essere tutta incollatura!
Sono gradite vostre esperienze sui parametri che utilizzate e se questi tipi di post sono utili per voi tutti.
L’adozione dell’alluminio come materiale prevalente nelle costruzioni moderne si colloca alla confluenza di innovazione tecnologica e sostenibilità ambientale, rendendolo una scelta strategica in un ere di crescente attenzione verso l’efficienza energetica e la riduzione dell’impatto ecologico delle opere edilizie. In questo contesto, le tecnologie Building Data Modeling (BIM) si presentano come un alleato cruciale per la progettazione, la gestione e la manutenzione delle strutture in alluminio. L’integrazione tra le proprietà uniche dell’alluminio e le potenti capacità di modellazione e simulazione offerte dal BIM permette non solo di ottimizzare i processi costruttivi, ma anche di migliorare la comunicazione tra i vari attori coinvolti nel ciclo di vita dell’opera, facilitando un approccio collaborativo e multidisciplinare. Questo articolo si propone di esplorare i vari aspetti di questa sinergia, evidenziando i vantaggi economici, operativi e ambientali che ne derivano, al fine di fornire un quadro esaustivo per professionisti e ricercatori interessati a queste tematiche.
Strutture in alluminio: caratteristiche tecniche e sostenibilità ambientale
Le strutture in alluminio si caratterizzano per diverse proprietà fisiche e meccaniche che le rendono particolarmente adatte a molteplici applicazioni nell’architettura e nell’ingegneria civile. Questo materiale, leggero e resistente, offre una notevole resistenza alla corrosione, il che contribuisce a una lunga durata nel tempo, riducendo la necessità di manutenzione frequente. Le sue proprietà di conduttività termica e elettrica lo rendono ideale per applicazioni che richiedono una buona performance energetica, mentre la sua versatilità permette di realizzare strutture personalizzate che soddisfano esigenze estetiche e funzionali specifiche.
In termini di sostenibilità ambientale, l’alluminio si distingue per la sua riciclabilità. Le strutture in alluminio possono essere facilmente recuperate e reinserite nel ciclo produttivo senza perdere le loro qualità intrinseche. Ciò consente un significativo risparmio energetico rispetto alla produzione di alluminio primario. Inoltre, l’uso di tecnologie BIM (Building Information Modeling) consente di ottimizzare il design delle strutture in alluminio, garantendo un’efficienza maggiore in termini di materiali e risorse utilizzate durante il processo costruttivo.
La sinergia tra strutture in alluminio e tecnologie BIM favorisce anche una gestione efficace del ciclo di vita degli edifici. Grazie alla modellazione tridimensionale e alla simulazione delle prestazioni, è possibile anticipare problematiche legate alla sostenibilità e all’impatto ambientale, con un accurato monitoraggio delle risorse spese. attraverso la pianificazione e l’ottimizzazione offerta dal BIM, i progettisti possono creare edifici più sostenibili e performanti, assicurando che le scelte progettuali siano in linea con i principi di economia circolare.
Caratteristiche Tecniche | Vantaggi Ambientali |
---|---|
Leggerezza | Minore consumo di energia nel trasporto |
Resistenza alla corrosione | Riduzione della necessità di riverniciatura |
Riciclabilità al 100% | Minimo spreco di risorse |
Efficienza energetica | Minor impatto ambientale complessivo |
Tecnologie BIM: definizione, applicazioni e impatti nel settore edilizio
Definizione delle tecnologie BIM
Le tecnologie BIM (Building Information Modeling) rappresentano un approccio innovativo per la progettazione, la costruzione e la gestione delle opere edili. La metodologia BIM consente di creare un modello digitale tridimensionale che integra informazioni dettagliate su ogni componente dell’edificio, facilitando la collaborazione tra i vari attori coinvolti nel processo. Attraverso l’uso di software specifici, i professionisti del settore possono visualizzare, analizzare e modificare i progetti in tempo reale, riducendo il rischio di errori e imprecisioni.
Applicazioni nel settore edilizio
Le tecnologie BIM trovano applicazione in diverse fasi del ciclo di vita di un progetto edilizio, dalle prime fasi di progettazione fino alla fase di gestione e manutenzione dell’edificio. Tra le applicazioni più significative, si evidenziano:
- Progettazione Architettonica: creazione di modelli dettagliati che facilitano la visualizzazione e l’analisi dei progetti.
- Coordinazione tra discipline: integrazione delle informazioni provenienti da ingegneria strutturale, impiantistica e architettura.
- Gestione della costruzione: ottimizzazione della pianificazione e monitoraggio delle attività in cantiere.
- Manutenzione e gestione degli asset: creazione di un database utili per la gestione a lungo termine degli immobili.
Impatto sul settore dell’alluminio
Nel contesto delle strutture in alluminio, l’integrazione delle tecnologie BIM offre significativi vantaggi. La capacità di modellare e simulare l’interazione tra elementi in alluminio e altre componenti del progetto consente di raggiungere una maggiore efficienza operativa. Le principali ripercussioni sono:
- Riduzione dei tempi di progettazione: grazie alla possibilità di visualizzare e testare vari scenari progettuali in un ambiente virtuale.
- Maggiore accuratezza nelle specifiche: ogni variazione o aggiornamento del progetto è immediatamente riflesso in tutte le componenti, garantendo coerenza.
- Ottimizzazione dei costi: identificazione precoce di problematiche costruttive, riducendo sprechi e migliorando la gestione delle risorse.
- Sostenibilità: l’analisi delle performance ambientali degli edifici consente scelte più consapevoli riguardo ai materiali e alle tecnologie utilizzate.
Tabelle comparativa dei vantaggi delle tecnologie BIM
Vantaggi | Tradizionale | BIM |
---|---|---|
Visualizzazione 3D | Limitata | Avanzata |
Collaborazione tra team | Complessità | facile integrazione |
Modifiche progettuali | Ritardi | Immediate |
Analisi dei costi | Posticipata | in tempo reale |
Integrazione delle strutture in alluminio nelle progettazioni BIM: un confronto tra metodologie tradizionali e innovative
la progettazione di strutture in alluminio all’interno di un contesto BIM offre un approccio innovativo rispetto alle metodologie tradizionali. L’integrazione nel processo costruttivo consente di affrontare in modo sistematico le problematiche legate alla sostenibilità, alla riduzione dei costi e all’ottimizzazione dei tempi di realizzazione. Una delle principali differenze tra i metodi tradizionali e quelli BIM risiede nella gestione dei dati: mentre nelle pratiche tradizionali si utilizzano documenti cartacei e disegni bidimensionali, il BIM promuove l’uso di modelli tridimensionali interattivi e di database digitali.
Un altro aspetto fondamentale è la collaborazione tra i vari attori del progetto. L’approccio BIM facilita la comunicazione tra architetti, ingegneri e appaltatori, permettendo una gestione più efficiente delle informazioni. Questo riduce il rischio di errori e conflitti durante le fasi esecutive. Le direzioni di cantiere possono acquisire e utilizzare modelli strutturali dettagliati in tempo reale, rendendo superfluo il ricorso a rilievi e verifiche manuali. Le fasi di controllo qualità diventano, quindi, più tempestive e semplici.
Quando si considerano i vantaggi nell’uso di strutture in alluminio attraverso BIM, emergono chiaramente i benefici riguardanti:
- Efficienza progettuale: analisi dei carichi e ottimizzazione delle sezioni
- Visualizzazione realistica: anticipazione delle problematiche attraverso modelli 3D interattivi
- Gestione della manutenzione: creazione di sistemi informativi per il monitoraggio continuo
- Sostenibilità ambientale: scelta di materiali e soluzioni costruttive a basso impatto
Dal punto di vista economico, l’utilizzo dell’alluminio associato a tecnologie BIM può ridurre significativamente i costi totali del progetto. Secondo alcune stime, l’adozione integrazione di questi metodi può comportare una riduzione dei costi del 15-25% rispetto ai metodi tradizionali. Inoltre,il risparmio energetico e la facilità di riciclo dell’alluminio generano un valore aggiunto nel lungo termine, contribuendo anche a una maggiore competitività sul mercato.
Vantaggio | Metodologia Tradizionale | Metodologia BIM |
---|---|---|
Efficacia nella pianificazione | Bassa | Alta |
Costi di gestione | Alti | Ridotti |
Collaborazione tra i team | Limitata | Eccellente |
Vantaggi della sinergia tra alluminio e BIM: efficienza, costi e gestione del ciclo vita delle costruzioni
La combinazione tra l’alluminio e le tecnologie BIM (Building Information Modeling) offre vantaggi significativi che incrementano l’efficienza operativa e la sostenibilità dei progetti edilizi. Questa sinergia permette un flusso di lavoro integrato, dove ogni fase del ciclo di vita di una costruzione può essere monitorata e ottimizzata. Grazie alla leggerezza e alla versatilità dell’alluminio, è possibile progettare strutture più agili, riducendo i tempi di costruzione e aumentando la funzionalità degli spazi.
Un altro aspetto fondamentale è la riduzione dei costi, sia iniziali che di gestione. L’utilizzo degli strumenti BIM facilita la creazione di modelli 3D dettagliati, contribuendo a:
- Ottimizzazione dei materiali: L’alluminio, essendo riciclabile al 100%, contribuisce a una gestione più efficace delle risorse e a una diminuzione degli sprechi durante la fase di costruzione.
- Identificazione precoce di errori: Il processo di progettazione tridimensionale consente di individuare problematiche strutturali prima che si manifestino in cantiere, abbattendo così i costi derivanti da riparazioni e modifiche.
- Previsione dei costi operativi: BIM permette di simulare le performance delle strutture in alluminio durante tutto il loro ciclo di vita, facilitando la pianificazione economica e la scelta di soluzioni più convenienti.
la gestione del ciclo di vita degli edifici è ulteriore prova dell’efficacia dell’integrazione tra alluminio e BIM. Attraverso un accurato monitoraggio delle prestazioni, è possibile pianificare interventi di manutenzione programmata e ristrutturazioni in modo da massimizzare la durata utile delle strutture. Inoltre, la capacità di generare report dettagliati facilitate il processo decisionale per la gestione efficiente degli asset edilizi.
Vantaggi | alluminio | BIM |
---|---|---|
Riduzione dei costi | Materiale riciclabile, minori spese per la produzione | Eliminazione di errori progettuali, risparmio in fase di cantiere |
Efficienza operativa | Strutture leggere e rapide da assemblare | Visualizzazione 3D e pianificazione delle fasi di lavoro |
Gestione sostenibile | Minimizzazione degli sprechi, riciclo completo | Analisi delle prestazioni durante l’intero ciclo di vita |
Domande e risposte
D: Cos’è il Building Information Modeling (BIM) e quali sono le sue principali caratteristiche?
R: Il Building Information Modeling (BIM) è un processo innovativo che implica la creazione e la gestione di informazioni digitali relative agli edifici e alle infrastrutture. Le principali caratteristiche del BIM includono la modellazione tridimensionale, l’integrazione di dati relativi a materiali, costi e tempistiche, nonché la capacità di simulare e analizzare le prestazioni strutturali e energetiche di un progetto. questa tecnologia consente un approccio collaborativo, migliorando la comunicazione tra i vari attori coinvolti nel progetto.
D: Qual è il ruolo delle strutture in alluminio nell’ambito del BIM?
R: Le strutture in alluminio rivestono un ruolo significativo nel contesto BIM grazie alla loro leggerezza, resistenza e versatilità. L’utilizzo di alluminio consente di progettare soluzioni architettoniche innovative e di ottimizzare le prestazioni energetiche degli edifici. Attraverso strumenti BIM, i progettisti possono simulare le proprietà fisiche e meccaniche dell’alluminio, facilitando l’integrazione con altri materiali e migliorando l’efficienza del processo di progettazione e costruzione.
D: Quali sono i principali vantaggi dell’integrazione tra strutture in alluminio e tecnologie BIM?
R: L’integrazione tra strutture in alluminio e tecnologie BIM offre numerosi vantaggi, tra cui:
- Ottimizzazione dei processi di progettazione: Lavorare con modelli BIM permette di realizzare progettazioni più accurate, riducendo gli errori e il tempo necessario per le modifiche.
- migliore pianificazione della costruzione: Le informazioni dettagliate e le simulazioni consentono di pianificare in modo più efficiente le fasi di costruzione, minimizzando i costi.
- Sostenibilità maggiore: L’alluminio è riciclabile e, unito alle capacità di analisi energetica del BIM, favorisce la progettazione di edifici sostenibili.
- Collaborazione enhanced: La comunicazione tra architetti, ingegneri e costruttori è facilitata, grazie alla piattaforma BIM che funge da riferimento comune per tutti i soggetti coinvolti.
D: In che modo le tecnologie BIM possono migliorare la sostenibilità delle strutture in alluminio?
R: Le tecnologie BIM contribuendo alla sostenibilità delle strutture in alluminio in diversi modi. Prima di tutto, BIM permette l’analisi delle prestazioni ambientali di un edificio e delle sue componenti, facilitando scelte progettuali più informate. Inoltre, grazie alla capacità di simulare diversi scenari, è possibile ottimizzare l’uso dell’alluminio, riducendo gli sprechi e aumentando l’efficienza nella fase di produzione. attraverso la gestione del ciclo di vita dell’edificio, il BIM consente di pianificare interventi di manutenzione e di miglioramento che estendono la durata dell’alluminio e minimizzano l’impatto ambientale globale.
D: Quali sono le sfide associate all’implementazione delle tecnologie BIM nel settore delle strutture in alluminio?
R: Sebbene i vantaggi dell’integrazione tra strutture in alluminio e BIM siano evidenti, ci sono alcune sfide da affrontare. Tra queste, la necessità di formazione e aggiornamento del personale, che deve acquisire competenze specifiche in materia di BIM. Inoltre, le aziende potrebbero dover investire in software avanzati e nella digitalizzazione dei processi, il che può rappresentare un onere finanziario. l’integrazione dei dati e delle informazioni da diverse fonti richiede standardizzazione e interoperabilità, condizioni cui le tecnologie BIM devono adeguarsi per funzionare in modo ottimale.
D: quali sviluppi futuri possono essere previsti per l’integrazione delle strutture in alluminio nel BIM?
R: Negli anni a venire, ci si aspetta un’evoluzione continua sia nell’ambito delle tecnologie BIM che nell’uso delle strutture in alluminio. È probabile che emergano strumenti più sofisticati per la modellazione e l’analisi, così come soluzioni software che offrano maggiore interoperabilità. Inoltre, l’attenzione crescente verso la sostenibilità e il riciclo potrà favorire un utilizzo più ampio dell’alluminio, promuovendo ricerche per migliorarne le proprietà e le applicazioni. L’integrazione tra BIM e tecnologie avanzate, come l’Intelligenza Artificiale e l’Internet delle Cose (IoT),porterà a nuove opportunità nel design e nella gestione degli edifici, rendendo le strutture in alluminio sempre più efficienti e sostenibili.
Conclusione
L’integrazione delle strutture in alluminio con le tecnologie BIM rappresenta una significativa evoluzione nel campo dell’architettura e dell’ingegneria. Attraverso l’impiego di strumenti digitali avanzati, è possibile ottimizzare la progettazione, favorire una migliore gestione delle risorse e migliorare la collaborazione tra i diversi attori del processo costruttivo. I vantaggi derivanti da questa sinergia non si limitano alla riduzione dei costi e dei tempi di realizzazione, ma si estendono anche a un incremento della sostenibilità ambientale e della durabilità delle opere realizzate. Di fronte a una crescente esigenza di innovazione e efficienza nel settore delle costruzioni, l’approccio integrato che combina strutture in alluminio e tecnologie BIM si rivela essenziale per affrontare le sfide contemporanee e per costruire un futuro più sostenibile. Il percorso di ricerca e sviluppo in questo ambito è appena iniziato, e le potenzialità offerte dalla digitalizzazione e dai materiali avanzati promettono di trasformare radicalmente il panorama dell’edilizia nel prossimo futuro.