Il futuro del taglio laser – prospettive e tecnologie emergenti
Il futuro del taglio laser – prospettive e tecnologie emergenti
Il taglio laser è una tecnologia avanzata che sta rivoluzionando l’industria manifatturiera grazie alla sua precisione, velocità ed efficienza. Consiste nell’utilizzo di un raggio laser concentrato per tagliare materiali con estrema precisione, eliminando la necessità di strumenti tradizionali come lame o frese. Questa tecnica offre una maggiore flessibilità nella progettazione e consente di lavorare su una vasta gamma di materiali, dal metallo alla plastica, con risultati sorprendenti.
Il taglio laser ha un’importanza cruciale nell’industria moderna, poiché incrementa la produttività, riduce gli sprechi di materiale e migliora la qualità dei prodotti finiti. Grazie alla sua precisione microscopica, questa tecnologia consente di realizzare pezzi complessi con dettagli minuziosi, che sarebbero altrimenti impossibili da ottenere con metodi tradizionali.
Sviluppi Attuali nel Taglio Laser
Miglioramenti nelle Prestazioni dei Laser
I recenti sviluppi nel campo del taglio laser hanno portato a significativi miglioramenti nelle prestazioni dei laser. Le nuove tecnologie hanno permesso di ottenere velocità di taglio maggiori, maggiore precisione e qualità di taglio superiore. Questi miglioramenti hanno reso il taglio laser una scelta sempre più vantaggiosa per una vasta gamma di applicazioni industriali.
Software e Controllo Intelligente nel Taglio Laser
Un aspetto fondamentale dei recenti sviluppi nel settore del taglio laser riguarda l’integrazione di software avanzati e sistemi di controllo intelligente. Queste tecnologie permettono di ottimizzare i processi di taglio, ridurre gli scarti di materiale e migliorare l’efficienza complessiva della produzione.
Il software e il controllo intelligente nel taglio laser sono in grado di monitorare costantemente le condizioni di lavorazione, regolare automaticamente i parametri di taglio in tempo reale e prevedere potenziali problemi prima che si verifichino. Questo porta a una maggiore precisione, affidabilità e velocità nei processi di taglio laser, offrendo vantaggi significativi alle aziende che investono in queste tecnologie all’avanguardia.
Materiali e Applicazioni Innovative
Nuovi Materiali per il Taglio Laser
In un contesto in cui l’innovazione è fondamentale, il settore del taglio laser si sta evolvendo rapidamente per poter lavorare nuovi materiali con precisione e affidabilità. Materiali come compositi avanzati, leghe metalliche speciali e materiali ibridi stanno diventando sempre più popolari per le applicazioni industriali. Grazie alla tecnologia laser, è possibile ottenere tagli puliti e precisi anche su questi materiali più complessi, aprendo nuove possibilità per la produzione di componenti di alta precisione.
Ampliamento degli Ambiti di Applicazione
L’utilizzo del taglio laser non è più limitato ai settori tradizionali come l’industria metalmeccanica e automobilistica. Grazie alle continue innovazioni tecnologiche, il taglio laser sta trovando sempre più spazio in settori come l’elettronica, l’aerospaziale, la produzione di dispositivi medici e persino nell’arte e nel design. Questa diversificazione degli ambiti di applicazione è resa possibile dalla versatilità e precisione del taglio laser, che consente di lavorare una vasta gamma di materiali in modo efficiente e accurato.
Tecnologie Emergenti nel Taglio Laser
Il Ruolo dell’Intelligenza Artificiale
L’intelligenza artificiale sta rivoluzionando il settore del taglio laser. Grazie all’uso di algoritmi complessi e sistemi di machine learning, le macchine per il taglio laser possono migliorare costantemente le proprie prestazioni, ottimizzando i parametri di taglio e riducendo gli errori. La capacità di adattamento e apprendimento delle macchine rende possibile ottenere tagli sempre più precisi e efficienti, garantendo risultati di alta qualità in tempi ridotti.
Integrazioni con la Stampa 3D e Il Mondo Digitale
Le integrazioni tra il taglio laser e la stampa 3D aprono nuove prospettive nel mondo della produzione. La combinazione di queste tecnologie permette la realizzazione di componenti complessi e personalizzati con estrema precisione. Inoltre, l’utilizzo di modelli digitali consente una maggiore flessibilità nella progettazione e nella produzione, riducendo i tempi e i costi legati alla lavorazione tradizionale.
Queste integrazioni accelerano l’innovazione e la personalizzazione dei prodotti, consentendo alle aziende di adattarsi rapidamente alle esigenze del mercato. Tuttavia, è fondamentale prestare attenzione alla sicurezza dei dati digitali e alla protezione della proprietà intellettuale in questo contesto tecnologico in continua evoluzione.
Sfide e Opportunità Future
Sostenibilità e Taglio Laser Ecosostenibile
Nel contesto attuale di crescente attenzione verso l’ambiente e la sostenibilità, il settore del taglio laser si trova di fronte alla sfida di ridurre l’impatto ambientale delle proprie attività. Una delle principali opportunità future è lo sviluppo di tecnologie per un taglio laser eco-sostenibile, che permetta di ridurre i consumi energetici e l’emissione di sostanze inquinanti, garantendo al contempo prestazioni elevate e di qualità.
La Formazione e Le Competenze del Futuro nel Settore
Con l’evolversi delle tecnologie nel settore del taglio laser, diventa fondamentale investire nella formazione e nello sviluppo delle competenze dei lavoratori. Il futuro del settore richiederà figure professionali in grado di gestire macchinari sempre più complessi, di utilizzare software avanzati e di adattarsi rapidamente a nuove soluzioni tecnologiche.
Inoltre, saranno necessarie competenze specifiche nell’ambito della programmazione dei macchinari, della manutenzione preventiva e della sicurezza sul lavoro, per garantire un’efficienza produttiva e un ambiente di lavoro sicuro e salutare.
Il Futuro del Taglio Laser – Prospettive e Tecnologie Emergenti
Il taglio laser rappresenta una tecnologia in continua evoluzione, con prospettive sempre più innovative e tecnologie emergenti che stanno rivoluzionando il settore. L’impiego di laser sempre più potenti e precisi, abbinati a sistemi di controllo avanzati, sta permettendo di ottenere risultati sempre più accurati e rapidi.
L’automazione dei processi e l’integrazione con sistemi intelligenti stanno influenzando in modo significativo il futuro del taglio laser, con previsioni di un’ulteriore crescita e diffusione in diversi settori industriali. È fondamentale rimanere costantemente aggiornati sulle nuove tecnologie e tendenze di mercato per rimanere competitivi e all’avanguardia in questo settore in costante evoluzione.
FAQ
Steel and aluminum tariffs have had a significant impact on the construction market in the United States. These tariffs were implemented by the Trump administration in an effort to protect domestic steel and aluminum industries from foreign competition. However, the tariffs have led to an increase in the cost of construction materials, making projects more expensive for builders and developers.
One of the key effects of the tariffs has been a rise in construction costs. Steel and aluminum are essential materials in construction, used in everything from structural beams to roofing materials. With the tariffs in place, the cost of these materials has gone up, leading to higher overall project costs. This has put a strain on construction companies, many of which are already operating on tight margins.
Another impact of the tariffs has been uncertainty in the market. Builders and developers rely on stable prices for materials in order to accurately estimate project costs and timelines. The fluctuating prices caused by the tariffs have made it difficult for companies to plan ahead and secure financing for their projects.
Despite these challenges, some industry experts see a silver lining in the tariffs. They argue that the tariffs have helped to revitalize domestic steel and aluminum industries, creating jobs and boosting the economy. However, others believe that the costs outweigh the benefits, and that the tariffs are ultimately hurting the construction market.
As the construction industry continues to navigate the effects of steel and aluminum tariffs, it is clear that these policies have had a significant impact on the market. Builders, developers, and other industry professionals will need to adapt to these changes in order to remain competitive in the evolving landscape of the construction market.
Le architetture metalliche nelle regioni polari rappresentano un’area di crescente interesse per gli architecti e gli ingegneri, in considerazione delle sfide ambientali e climatiche uniche che caratterizzano questi territori estremi. Le condizioni di temperatura rigida, le forti nevicate e i venti intensi richiedono l’adozione di materiali innovativi e strategie progettuali avanzate, capaci di garantire non solo la funzionalità e la sicurezza degli edifici, ma anche la sostenibilità. Questo articolo si propone di esaminare le peculiarità delle architetture metalliche in contesti polari, analizzando le proprietà dei materiali metallici impiegati e le tecniche costruttive più all’avanguardia. Attraverso una disamina approfondita delle principali soluzioni progettuali e delle recenti innovazioni tecnologiche, si intende fornire un contributo significativo alla comprensione delle dinamiche costruttive in ambienti estremi, evidenziando l’importanza di un approccio multidisciplinare che unisca architettura, ingegneria e scienze ambientali.
Materiali innovativi per la costruzione di strutture metalliche nelle regioni polari
La progettazione di strutture metalliche nelle regioni polari richiede l’impiego di materiali innovativi, capaci di resistere alle estreme condizioni climatiche e di garantire la longevità delle costruzioni. Tra le soluzioni più promettenti, si evidenziano i seguenti materiali:
- Acciaio Inox: Caratterizzato da un’elevata resistenza alla corrosione, è particolarmente adatto per le strutture esposte a fattori atmosferici estremi e all’azione del ghiaccio.
- Aluminio Leggero: Grazie alla sua leggerezza e resistenza, offre vantaggi significativi in termini di trasportabilità e facilità di assemblaggio, senza compromettere la stabilità.
- Materiali Compositi: L’uso di fibre di carbonio e resine termoindurenti consente di ottenere strutture ultra-resistenti e leggere, capaci di sopportare carichi elevati senza cedimenti.
- Acciaio a Bassa Temperatura: Specialmente trattato per mantenere le sue proprietà meccaniche anche a temperature estremamente basse,è ideale per le costruzioni in zone particolarmente fredde.
Un altro aspetto fondamentale è la metodologia costruttiva. Le tecnologie di assemblaggio modulari rappresentano un’alternativa efficiente, in quanto consentono di ridurre i tempi di costruzione e aumentare la precisione nell’assemblaggio. I settori modulari, concepiti per resistere a stress meccanici e termici, possono essere trasportati e assemblati in loco, minimizzando l’impatto ambientale.
Materiale | Caratteristiche | Applicazioni |
---|---|---|
Acciaio Inox | Resistente alla corrosione | Strutture esposte |
Aluminio Leggero | elevata leggerezza | Trasporti e assemblaggi |
Materiali Compositi | Ultra-resistenti | Strutture portanti |
Acciaio a Bassa Temperatura | Proprietà meccaniche stabili | Costruzioni in climi estremi |
Inoltre, le recenti innovazioni nella nanotecnologia e nella metallurgia permettono di sviluppare leghe ad alte prestazioni, che possono migliorare ulteriormente la resistenza e la durata delle strutture. Queste leghe speciali offrono soluzioni per situazioni specifiche, come la protezione dalle fratture dovute a sollecitazioni cicliche e dalle temperature termiche estreme.
è fondamentale considerare l’integrazione di sistemi di isolamento termico avanzati. Questi sistemi non solo migliorano il comfort interno, ma contribuiscono anche all’efficienza energetica degli edifici, riducendo il fabbisogno di riscaldamento e il conseguente impatto ambientale.
Strategie di progettazione per la resistenza alle condizioni estreme in ambienti artici
Progettare per la resilienza in ambienti artici richiede un approccio multidisciplinare che integra ingegneria, architettura e scienze ambientali. Le condizioni estreme, caratterizzate da temperature rigide, venti forti e accumuli nevosi significativi, impongono scelte progettuali innovative e l’adozione di materiali avanzati.Risultano fondamentali diverse strategie di progettazione, tra cui:
- Ottimizzazione della forma: Le geometrie arrotondate e aerodinamiche sono preferite per ridurre l’impatto dei venti e minimizzare la raccolta di neve, facilitando così la manutenzione.
- Isolamento termico avanzato: Utilizzare materiali ad alte prestazioni, come schiume poliuretaniche o materiali compositi, per garantire un elevato isolamento termico, riducendo al contempo il consumo energetico.
- Fondazioni profonde: Per affrontare lo scioglimento del permafrost, è essenziale progettare fondazioni che raggiungano strati stabili, evitando il cedimento strutturale.
- Rivestimenti resistenti all’erosione: L’uso di rivestimenti metallici trattati chimicamente può offrire una resistenza migliorata alla corrosione e all’erosione causate dal tempo e dagli agenti atmosferici.
- Integrazione di tecnologie sostenibili: Incorporare sistemi di energia rinnovabile,come pannelli solari e turbine eoliche,può garantire autonomia energetica e sostenibilità durante le operazioni in aree remote.
Un ulteriore aspetto da considerare è la gestione delle risorse idriche. La raccolta di acqua piovana e la gestione dello scioglimento dei ghiacci sono cruciali per garantire approvvigionamento idrico, specialmente nelle strutture isolate. Inoltre, l’applicazione di sistemi di drenaggio progettati per monitorare e controllare l’acqua di fusione può prevenire il deterioramento delle strutture.
È anche essenziale enfatizzare la formazione e sensibilizzazione del personale in merito alle condizioni locali. Il team di operazione deve essere equipaggiato non solo con le conoscenze tecniche necessarie, ma anche con una comprensione approfondita delle dinamiche ambientali e climatiche tipiche della regione artica. L’introduzione di programmi di formazione specifici può migliorare notevolmente la sicurezza operativa e l’efficacia nella gestione delle emergenze.
Per facilitare una migliore comprensione delle sfide e delle soluzioni, la seguente tabella riassume i materiali e le loro proprietà chiave utilizzati nella costruzione di architetture resistenti in ambienti artici:
Materiale | Proprietà | Applicazione |
---|---|---|
Acciaio inossidabile | Resistente alla corrosione, durevole | Strutture portanti e rivestimenti |
Legno lamellare | Buone proprietà isolanti, flessibile | Elementi strutturali e facciate |
Pannelli sandwich | Leggeri, eccellente isolamento | Pareti prefabbricate |
Materiali termoplastici | Resistenti a basse temperature | Rivestimenti e finiture esterne |
Calcestruzzo speciale | Resistente al gelo, alta durabilità | Fondazioni e strutture di supporto |
l’approccio progettuale per affrontare le condizioni estreme in ambienti artici deve essere olistico, tenendo conto delle interazioni tra struttura, materiali e ambiente. Solo così è possibile garantire la longevità e la sicurezza delle architetture metalliche in queste regioni inospitali.
Tecnologie sostenibili e riduzione dellimpatto ambientale nellarchitettura poliartica
Negli ambienti estremi delle regioni polari, è imperativo adottare tecnologie sostenibili per ridurre l’impatto ambientale delle costruzioni architettoniche. L’uso di materiali innovativi e strategie progettuali può garantire non solo la durabilità degli edifici, ma anche il rispetto delle normative ecologiche. In questo contesto, è fondamentale considerare alcune pratiche chiave.
- Utilizzo di materiali riciclati: L’impiego di acciaio e alluminio riciclati può contribuire a ridurre l’impatto del ciclo di vita del materiale, diminuendo le emissioni di carbonio associate alla produzione di nuovi metalli.
- Ottimizzazione energetica: Progettare edifici che integrino fonti di energia rinnovabile, come il solare termico e fotovoltaico, consente un’autosufficienza energetica che è cruciale in contesti isolati.
- Progettazione passiva: Le tecniche di progettazione passiva sfruttano le condizioni ambientali locali, massimizzando la luce naturale e il riscaldamento passivo, riducendo così il fabbisogno energetico.
La scelta di tecnologie come i sistemi di isolamento avanzati gioca un ruolo essenziale nella sostenibilità degli edifici polari. Questi sistemi non solo proteggono dagli inverni rigidi sono anche progettati per ottimizzare le risorse energetiche. È possibile identificare alcune soluzioni efficaci:
Tipo di Isolamento | vantaggi |
---|---|
Poliuretano | Alta resistenza termica e leggerezza. |
Fibra di legno | Materiale naturale e biodegradabile. |
Perlite espansa | Resistente al fuoco e ottima coibentazione. |
Implementare un approccio di design circolare è un altro passo fondamentale verso la sostenibilità. Ciò significa progettare gli edifici con la possibilità di smontarli, riutilizzando i materiali e riducendo i rifiuti. Inoltre, pratiche di costruzione che rispettano il principio della biorifinitura possono contribuire significativamente a minimizzare l’influenza sull’ecosistema locale.
la sensibilizzazione e il coinvolgimento delle comunità locali nella progettazione e nella realizzazione degli edifici possono trasformare il processo costruttivo in un’attività sostenibile e rispettosa, promuovendo l’uso di risorse locali e tradizioni architettoniche. Questa sinergia non solo migliora le relazioni sociali, ma incarna un vero esempio di architettura responsabile e a lungo termine nelle regioni polari.
Esempi di best practices e casi studio di edifici metallici nelle regioni estreme
Le sfide che gli edifici metallici affrontano nelle regioni estreme richiedono un approccio progettuale innovativo, incentrato sull’uso di materiali avanzati e strategie di costruzione versatile. Vari esempi dimostrano come le tecniche moderne possano superare le limitazioni degli ambienti rigidi.
Una delle best practices più efficaci è l’uso di leghe leggere di alluminio, che offrono resistenza alla corrosione e un elevato rapporto resistenza-peso. Questi materiali sono particolarmente adatti per costruzioni in aree con forti venti e temperature estreme. Alcuni esempi pratici includono:
- Base di ricerca Amundsen-scott, Antarctica: Utilizza una struttura in acciaio coibentato per resistere a temperature inferiori a -50 gradi Celsius.
- Stazione di ricerca Barneo, Russia: Montata su una piattaforma galleggiante, adotta l’alluminio per minimalizzare il peso e ottimizzare la resistenza ai carichi di neve.
- Centro polare di ricerca Ny-Ålesund, Svalbard: Impiega un involucro metallico progettato per riflettere la luce solare e massimizzare il riscaldamento passivo.
Un altro aspetto cruciale nella progettazione di edifici metallici nelle regioni polari è la considerazione delle caratteristiche termiche e dell’isolamento. L’utilizzo di sistemi modulari consente una maggiore adattabilità e una rapida costruzione, importante in situazioni di emergenza.
Le seguenti case studio esemplificano come l’innovazione ingegneristica e l’attenzione al dettaglio possano portare a soluzioni ottimali:
Nome del Progetto | Anno di Completamento | Struttura Usata |
---|---|---|
Stazione di Ricerca Concordia | 2005 | Acciaio Inossidabile e Polistirolo espanso |
Base di Ricerca unificata PSF | 2010 | Alluminio Strutturale |
Centro di Sperimentazione Artica | 2018 | Acciaio Zincato con Coibentazione Avanzata |
è fondamentale l’adozione di strategie sostenibili durante l’intero ciclo di vita dell’edificio. La riduzione dell’impatto ambientale è migliorata attraverso:
- Utilizzo di energie rinnovabili, come i pannelli solari, che sono state integrate in edifici metallici per ottimizzare l’autosufficienza energetica.
- Gestione dell’acqua piovana attraverso sistemi di raccolta e filtrazione, contribuendo a mantenere l’equilibrio ecologico dell’area.
- Implementazione di tecnologie smart per un controllo in tempo reale delle condizioni climatiche e per l’ottimizzazione del consumo energetico.
in Conclusione
L’analisi delle architetture metalliche nelle regioni polari evidenzia l’importanza di una progettazione che integri materiali all’avanguardia e strategie innovative per affrontare le sfide estreme di questi ambienti. L’utilizzo di leghe metalliche resistenti alla corrosione e alle condizioni climatiche avverse, unito a tecniche costruttive che valorizzano l’efficienza energetica e la sostenibilità, rappresenta un passo fondamentale verso la realizzazione di strutture funzionali e durature.
Le ricerche continuative in questo settore sono essenziali per sviluppare soluzioni sempre più avanzate, in grado di rispondere alle esigenze di abitabilità e operatività in contesti così critici. È auspicabile che future indagini multidisciplinari possano approfondire le interazioni tra materiali, progettazione e ambiente, promuovendo un approccio olistico che possa ispirare nuove generazioni di architetti e ingegneri. Solo attraverso un continuo dialogo tra teoria e pratica sarà possibile affrontare le sfide poste dalle architetture metalliche in regioni polari, contribuendo così a una migliore comprensione dei nostri limiti e delle potenzialità insite nella costruzione in ambienti estremi.
Introduzione
Negli ultimi anni, il settore dell’edilizia ha assistito a una crescente innovazione, con particolare attenzione alle tecnologie di prefabbricazione. Tra i materiali che stanno guadagnando spazio nel panorama costruittivo moderno, l’alluminio si distingue per le sue proprietà uniche e versatili. Le strutture in alluminio, grazie alla loro leggerezza, resistenza alla corrosione e facilità di lavorazione, si prestano in modo eccellente a metodologie prefabbricate, permettendo non solo una significativa riduzione dei tempi di costruzione, ma anche un miglioramento dell’efficienza energetica e una diminuzione degli sprechi material. Questo articolo si propone di esaminare le tecniche di prefabbricazione più avanzate per le strutture in alluminio, analizzando i vantaggi, le criticità e le prospettive future di un approccio che si colloca all’intersezione tra innovazione tecnologica e sostenibilità ambientale. Attraverso un’analisi approfondita delle metodologie attuali e dei casi studio, cercheremo di delineare il ruolo cruciale che le strutture prefabbricate in alluminio possono avere nel delineare il futuro dell’architettura e dell’ingegneria moderna.
Analisi delle Proprietà Strutturali dellAlluminio nella Prefabbricazione
L’alluminio,grazie alle sue proprietà intrinseche,si è affermato come materiale chiave nella prefabbricazione. La sua leggerezza, abbinata a un’elevata resistenza alla corrosione, consente di realizzare strutture che non solo soddisfano requisiti estetici, ma anche funzionali.La relazione tra peso e resistenza dell’alluminio è particolarmente vantaggiosa in ambiti dove la riduzione del carico complessivo è imperativa.
La resistenza meccanica dell’alluminio è influenzata da vari fattori, tra cui la lega utilizzata e il processo produttivo adottato. le leghe più comuni, come la serie 6000 e 7000, offrono un mix ideale di resistenza e lavorabilità. Tra le principali proprietà strutturali si possono evidenziare:
- Elevata resistenza alla trazione: Questa caratteristica permette di utilizzare meno materiale per ottenere strutture robuste.
- Buona duttilità: Consente di modellare l’alluminio in forme complesse senza rischio di fratture.
- ottima conducibilità termica ed elettrica: Indispensabile in applicazioni industriali e infrastrutture.
- Resistenza alla corrosione: L’alluminio forma uno strato di ossido che lo protegge, aumentando la durabilità dell’elemento prefabbricato.
Incorporare l’alluminio nella prefabbricazione consente anche di ottimizzare i costi e ridurre i tempi di costruzione. Utilizzando processi come il taglio al plasma e la saldatura avanzata, è possibile ottenere componenti prefabbricati che richiedono una minima lavorazione in loco.Il seguente schema riassuntivo espone alcuni vantaggi della prefabbricazione in alluminio:
Vantaggi | Descrizione |
---|---|
Velocità di costruzione | Componenti pronti all’uso riducono i tempi di assemblaggio sul sito. |
Efficienza dei costi | Minori spese operative grazie alla riduzione degli scarti e all’ottimizzazione dei materiali. |
sostenibilità | L’alluminio è riciclabile, contribuendo a un’opzione costruttiva più eco-compatibile. |
Tecniche di Assemblaggio e Lavorazione per Strutture Prefabbricate in Alluminio
La prefabbricazione delle strutture in alluminio si distingue per l’utilizzo di tecniche avanzate che ottimizzano sia il processo produttivo che la qualità finale del prodotto. Tra le tecniche più diffuse troviamo:
- Taglio e Piegatura: Processi altamente precisi che permettono di ottenere componenti strutturali conformi alle specifiche progettuali.L’uso di macchinari CNC (controllo numerico computerizzato) garantisce tolleranze minime.
- Saldatura: Le saldature TIG (tungsten inert gas) e MIG (metal inert gas) sono particolarmente diffuse nella lavorazione dell’alluminio, grazie alla loro capacità di assicurare giunzioni forti e durevoli.
- Trattamenti Superficiali: Tecniche di anodizzazione e verniciatura sono impiegate per migliorare la resistenza alla corrosione e per personalizzare esteticamente le strutture.
Un’altra fase fondamentale nella prefabbricazione delle strutture in alluminio è l’assemblaggio. Questo può avvenire tramite diversi metodi, a seconda del design e dell’applicazione finale. I metodi prediletti includono:
- Assemblaggio meccanico: L’uso di viti, bulloni e rivetti che consente un montaggio semplice e una facile manutenzione.
- Assemblaggio incollato: Impiego di adesivi strutturali che offrono vantaggi estetici e facilitano processi di montaggio più rapidi.
Le richiedono una gestione accurata del progetto, che può includere l’uso di software di modellazione 3D per visualizzare e simulare le diverse fasi operative. Questo approccio integrato non solo riduce i tempi di costruzione, ma aumenta anche la precisione del prodotto finale, minimizzando gli sprechi di materiale.
Un riferimento utile per comprendere l’efficacia delle varie tecniche di assemblaggio è la seguente tabella che confronta i metodi in termini di applicazione e vantaggi:
Metodo di Assemblaggio | Applicazione | Vantaggi |
---|---|---|
Meccanico | Strutture modulari | Facilità di manutenzione |
Incollato | Elementi estetici | Finitura pulita |
Saldato | Strutture portanti | Elevata resistenza |
Innovazioni tecnologiche nelle Applicazioni delle Strutture in Alluminio
Negli ultimi anni, l’evoluzione delle tecnologie di progettazione e produzione ha permesso di ottenere significativi progressi nelle strutture in alluminio. L’applicazione di metodologie innovative come il modelling parametrico e la fabbricazione digitale ha reso possibile la creazione di componenti più complessi e leggermente interconnessi senza compromettere la resistenza o la durabilità delle strutture. Questo approccio consente una personalizzazione su misura, rispondendo efficacemente alle esigenze architettoniche contemporanee.
Inoltre, la prefabbricazione delle strutture in alluminio si avvale di sistemi automatizzati che ottimizzano i tempi di produzione e riducono gli sprechi. Tra le innovazioni più rilevanti possiamo includere:
- Robotica Avanzata: L’uso di robot per la lavorazione e l’assemblaggio consente di migliorare la precisione e la coerenza qualitativa delle strutture.
- Stampaggio 3D: Tecnologie di stampa 3D specifiche per metalli permettono la realizzazione di elementi anche complessi in un unico passaggio di produzione riducendo i costi e aumentando la velocità.
- materiali Compositi: L’uso di leghe leggere e materiali compositi che si affiancano all’alluminio offre opzioni progettuali uniche, aumentando la resistenza senza pesi eccessivi.
Un’importante area di sviluppo riguarda anche l’efficienza energetica nelle applicazioni delle strutture prefabbricate. Grazie all’integrazione di sistemi intelligenti per la gestione delle energie rinnovabili, è possibile creare edifici che non solo riducono il fabbisogno energetico, ma generano in parte la propria energia. Attraverso l’uso di pannelli fotovoltaici integrati e sistemi di isolamento avanzati, le strutture in alluminio contribuiscono a un’architettura sostenibile.
Le seguenti informazioni riassumono alcune delle principali applicazioni delle innovazioni nelle strutture in alluminio:
Applicazione | Vantaggi |
---|---|
Edifici Residenziali | Leggerezza e resistenza, facilitando la costruzione in spazi urbani ristretti. |
Strutture Pubbliche | Design contemporaneo, adattabilità a diverse esigenze funzionali. |
Infrastrutture per Trasporti | Durabilità nel tempo e resistenza agli agenti atmosferici. |
Sostenibilità e Impatti Ambientali delle Strutture Prefabbricate in Alluminio
Le strutture prefabbricate in alluminio rappresentano una soluzione innovativa e sostenibile nel settore dell’edilizia. La loro costruzione riduce notevolmente l’impatto ambientale rispetto alle tecniche tradizionali, grazie a diverse caratteristiche distintive. In primo luogo, l’alluminio è un materiale altamente riciclabile e riutilizzabile, il che diminuisce la necessità di estrazione di nuove materie prime e abbassa le emissioni di CO2 associate alla produzione. Il ciclo di vita di un edificio prefabbricato in alluminio si traduce quindi in un consumo energetico significativamente inferiore.
In aggiunta, la prefabbricazione consente una pianificazione più efficiente delle risorse e dei processi produttivi.Questo porta a una riduzione degli sprechi grazie all’uso controllato dei materiali durante la costruzione. Le tecniche di assemblaggio utilizzate nei processi prefabbricati garantiscono anche una maggiore precisione, limitando le lavorazioni superflue e facendo del site management un’attività più sostenibile. L’ottimizzazione delle tempistiche di costruzione significa altresì ridurre l’impatto ambientale associato ai cantieri, come l’inquinamento acustico e atmosferico.
Un altro aspetto cruciale delle strutture in alluminio riguarda la loro longevità e resistenza.La durabilità di questo materiale implica costi di manutenzione ridotti e una minore necessità di riparazioni, fattori che contribuiscono a prolungare la vita utile degli edifici e ridurre il turnover delle strutture: un vantaggio significativo in un’ottica di sostenibilità.
Vantaggi delle Strutture Prefabbricate in Alluminio | Impatto Ambientale |
---|---|
Riciclabilità | Riduzione dell’uso di nuove materie prime |
Efficienza costruttiva | Minor spreco di materiali |
Durabilità | Minori interventi di manutenzione |
Rapidità di montaggio | Riduzione dell’impatto da cantiere |
Domande e Risposte
Q&A: Strutture in alluminio: Tecniche per la Prefabbricazione
Domanda 1: Quali sono i vantaggi dell’utilizzo dell’alluminio nella prefabbricazione delle strutture?
Risposta: L’alluminio presenta numerosi vantaggi nell’ambito della prefabbricazione, tra cui un elevato rapporto resistenza-peso, che consente di realizzare strutture leggere ma robuste. Inoltre, la sua resistenza alla corrosione riduce i costi di manutenzione e allunga la vita utile delle costruzioni. La versatilità di questo materiale permette anche la realizzazione di forme complesse e un’estetica moderna, aumentando le possibilità progettuali.
Domanda 2: Quali tecniche di prefabbricazione sono maggiormente utilizzate per le strutture in alluminio?
Risposta: Le tecniche di prefabbricazione per strutture in alluminio includono la produzione di moduli prefabbricati, la saldatura di elementi strutturali e l’assemblaggio di pannelli. Tra i metodi più innovativi troviamo anche l’uso della stampa 3D per la realizzazione di componenti specifici,che consente una personalizzazione elevata e una riduzione dei tempi di produzione. L’integrazione di tecnologie digitali e sistemi di progettazione assistita (CAD) rappresenta una fase cruciale per garantire precisione e ripetibilità.
Domanda 3: In che modo la prefabbricazione in alluminio contribuisce alla sostenibilità ambientale?
Risposta: La prefabbricazione in alluminio può evidenziare un impatto positivo sulla sostenibilità grazie alla riduzione dei rifiuti di cantiere e all’efficienza energetica durante la fase di costruzione. L’alluminio è altamente riciclabile, con il 75% dell’alluminio mai prodotto che è ancora in uso, il che ne migliora ulteriormente l’impatto ambientale. Inoltre,le strutture prefabbricate in alluminio possono essere progettate per massimizzare l’efficienza energetica,grazie a sistemi di isolamento termico avanzati.
Domanda 4: Quali sono le sfide associate alla prefabbricazione di strutture in alluminio?
Risposta: Tra le sfide principali vi è la necessità di investire in tecnologie avanzate e competenze specialistiche nel processo produttivo. La lavorazione dell’alluminio richiede attrezzature specifiche e esperti con abilità tecniche elevate. Un’altra sfida è rappresentata dai costi iniziali di produzione, che possono risultare elevati. Inoltre, è essenziale garantire la qualità e la sicurezza dei moduli prefabbricati, necessitando di rigorosi controlli di qualità.Domanda 5: Quali sono le prospettive future per l’utilizzo dell’alluminio nella prefabbricazione?
Risposta: Le prospettive per l’utilizzo dell’alluminio nella prefabbricazione appaiono positive,grazie all’evoluzione delle tecnologie di produzione e all’aumento della consapevolezza ambientale. Ci si aspetta un incremento nella domanda di strutture prefabbricate leggere ed eco-sostenibili, parallelo all’espansione delle normative che promuovono la costruzione sostenibile. L’innovazione nella progettazione attraverso l’uso di software avanzati e metodologie di costruzione modulari potrebbe ulteriormente spingere l’adozione di strutture in alluminio nel settore edile.
In conclusione
l’analisi delle strutture in alluminio e delle tecniche di prefabbricazione evidenzia non solo l’efficienza e la versatilità di questo materiale, ma anche il potenziale innovativo che offre nel contesto delle costruzioni moderne. Le tecnologie di prefabbricazione, integrate con l’alluminio, permettono di ottimizzare i tempi di costruzione, garantire una maggiore sostenibilità e ridurre i costi operativi, rendendo questi approcci sempre più rilevanti nell’architettura contemporanea.
È cruciale che i professionisti del settore continuino a esplorare e sperimentare con queste tecniche, promuovendo l’evoluzione di metodi costruttivi che rispondano alle esigenze di un mercato in continua trasformazione. L’interdisciplinarità tra ingegneria, design e sostenibilità sarà fondamentale per affrontare le sfide future e contribuire a un ambiente costruito più efficiente e ben progettato.
Pertanto, la ricerca e l’adozione di soluzioni innovative nel campo delle strutture in alluminio non sono semplicemente utili, ma si dimostrano essenziali per l’avanzamento del settore edilizio nel suo complesso.Invitiamo,quindi,accademici,ingegneri e architetti a collaborare per massimizzare i benefici offerti da queste tecnologie,colmando il divario tra teoria e pratica e spingendo verso un futuro costruito più responsabile e all’avanguardia.
Ing. Stefano Migliardi
In questo primo post vorrei condividere con voi un aspetto che riguarda la qualità della
saldatura metallica ed in particolare la scelta di 2 dei 3 parametri (il terzo è la velocità) fondamentali
nell’impostazione del lavoro.
Generalmente si lavora con una WPS di riferimento (nei prossimi post inserisco qualche esempio).
Ma quando si comincia un giunto è importante tarare il mix di Ampère e Volt perché ognuno di essi ha un
significato ben preciso.
Gli Ampère, cioè la corrente, incidono sulla profondità e fusione del giunto; i Volt cioè la tensione incidono sulla forma del cordone.
Quindi a Volt fissi, se aumento gli ampere aumento la profondità/penetrazione (potrebbe essere eccessiva!) (foto da primeweld.com)
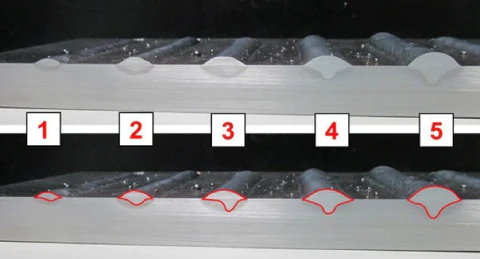
Invece ad Ampère fissi, se aumento i Volt (es. 23-29-35 ecc.) il giunto sarà sempre più largo come forma.

Perciò ad esempio su un tipico giunto a T saldato da un lato, MAG, S275JR, sp. 12 con 12 mm, posizione
frontale PB a banco, multipass, per avere una buona fusione al vertice si può selezionare:
1° passata SPRAY ARC e si sta sui 220/240 A e 23/24 Volt e si va sui 220/240 mm/min
Altre passate SPRAY ARC e si sta sui 220/240 A e 23/24 Volt ma si va più veloci sui 290/320 mm/min
Quindi ad un esame di patentino o in generale nel lavoro, nella valutazione del giunto, fate attenzione se la macchina è impostata su SHORT ARC o su SPRAY ARC perché i parametri V e A sono differenti.
Sicuramente la “mano” del saldatore è fondamentale ma non è detto che una bella maglia di saldatura vuole dire fusione certa perché può essere tutta incollatura!
Sono gradite vostre esperienze sui parametri che utilizzate e se questi tipi di post sono utili per voi tutti.
L’arte della saldatura TIG (Tungsten Inert Gas) si presenta come una delle tecniche più sofisticate e versatili nel campo della lavorazione dei metalli, in particolare per le strutture in alluminio. questo metodo di saldatura, caratterizzato dall’utilizzo di un elettrodo di tungsteno e da un’atmosfera di gas inerte, consente di ottenere giunzioni di elevata qualità, minimizzando il rischio di contaminazione e deformazione del materiale. L’alluminio, per le sue proprietà peculiari quali leggerezza, resistenza alla corrosione e facilità di lavorazione, è diventato un materiale di riferimento in settori quali l’industria aeronautica, automobilistica e architettonica. Tuttavia, la saldatura di tale metallo presenta sfide specifiche, che richiedono competenze tecniche e conoscenze approfondite sui processi termici e le interazioni materiali. In questo articolo, si esaminerà in dettaglio l’importanza della saldatura TIG nelle strutture in alluminio, evidenziando le tecniche, le applicazioni e le considerazioni pratiche necessarie per garantire risultati ottimali in contesti industriali e artigianali.
Tecniche Avanzate di Saldatura TIG per l’Alluminio Strutturale
La saldatura TIG rappresenta una delle tecniche più avanzate e versatili per unire strutture in alluminio, essenziale per garantire la resistenza e l’integrità delle applicazioni strutturali. Per eseguire una saldatura TIG di alta qualità, è fondamentale padroneggiare vari aspetti tecnici, tra cui la scelta dei materiali, la preparazione delle superfici e l’ottimizzazione dei parametri di saldatura.
Le fasi fondamentali della saldatura TIG per strutture in alluminio includono:
- Preparazione del materiale: Rimuovere contaminazioni e ossidi dalle superfici da saldare.
- Scelta dell’elettrodo: L’uso di elettrodi di tungsteno con una punta appropriata può migliorare la qualità della saldatura.
- Parametri di saldatura: L’ottimizzazione di corrente, tensione e velocità di avanzamento è cruciale per evitare difetti.
Una corretta tecnica di saldatura è altrettanto importante. la posizione dell’elettrodo deve essere mantenuta costante per garantire una fusione adeguata. Inoltre, la tecnica di movimento, che può variare da un percorso lineare a uno a zig-zag, influisce significativamente sulla penetrazione e sull’aspetto finale della saldatura. A tal proposito, ecco un confronto tra diverse tecniche di saldatura TIG:
Tecnica | Vantaggi | Svantaggi |
---|---|---|
Movimento Lineare | penetrazione uniforme e meno rischi di surriscaldamento | Richiede maggiore controllo della mano |
Movimento a Zig-Zag | Adatta per giunzioni più spesse e miglior riempimento | Può causare surriscaldamento localizzato |
la scelta del filler metal gioca un ruolo cruciale in ogni saldatura TIG per l’alluminio. Utilizzare una lega compatibile con il materiale base è fondamentale per garantire la qualità e la resistenza della saldatura. L’impiego di filler con determinate caratteristiche chimiche e meccaniche permette, infatti, di ottenere giunzioni più robuste, adatte a sopportare sollecitazioni elevate in ambito strutturale.
Caratteristiche dei Materiali e Scelte degli Elettrodi
La selezione dei materiali per la saldatura TIG, in particolare per le strutture in alluminio, gioca un ruolo cruciale nella qualità e nella durabilità dei legami. L’alluminio, noto per la sua leggerezza e resistenza alla corrosione, richiede una comprensione approfondita delle sue proprietà fisiche e chimiche. Tra le caratteristiche più rilevanti della saldatura di questo metallo si possono citare:
- Conduttività Termica: l’alluminio ha un’elevata conduttività termica, il che implica una rapida dispersione del calore durante il processo di saldatura.
- Resistenza alla corrosione: è fondamentale scegliere materiali e rivestimenti che non compromettano questa caratteristica intrinseca dell’alluminio.
- Formabilità: la modalità di saldatura deve considerare la capacità dell’alluminio di deformarsi senza fratture.
Quando si parla di elettrodi per la saldatura TIG, la scelta è determinante per ottenere risultati ottimali. Gli elettrodi in tungsteno sono i più comunemente utilizzati, grazie alla loro alta resistenza al calore e all’abrasione. È essenziale considerare vari fattori per una corretta selezione:
- Tipo di Tungsteno: gli elettrodi possono essere pure o legati, ognuno con specifiche applicazioni. Gli elettrodi legati con terre rare,come il lanthanum, offrono una stabilità dell’arco migliore.
- Dimensione dell’Elettrodo: la dimensione dovrebbe essere scelta in base allo spessore del materiale da saldare e alla corrente utilizzata.
- Preparazione dell’Elettrodo: una corretta punta affilata è essenziale per garantire un arco stabile e una penetrazione omogenea.
Inoltre, la posizione di saldatura e le tecniche di alimentazione della polvere di filler influenzano la scelta degli elettrodi e dei materiali. A tal proposito, una tabella riassuntiva delle opzioni disponibili può essere utile per confrontare le diverse possibilità:
Tipo di Elettrodo | Applicazione | Vantaggi |
---|---|---|
Tungsteno puro | Saldature leggere | Facile da affilare, costo contenuto |
Tungsteno legato (Lanthanum) | Saldature ad alta corrente | Stabilità dell’arco eccellente |
Tungsteno legato (Cerium) | Saldature generali | Buona resistenza alla corrosione |
comprendere queste caratteristiche e scelte consente una saldatura più precisa e duratura, garantendo così strutture in alluminio con ottime prestazioni meccaniche e di resistenza. La coordinazione tra materiali e tecniche di saldatura costituisce il fulcro del successo in questo ambito altamente specializzato.
Controllo dei Parametri di Saldatura e la Qualità del Giunto
Il controllo dei parametri di saldatura è fondamentale per garantire la qualità del giunto nelle applicazioni di saldatura TIG su strutture in alluminio. Ogni variabile, come la corrente, la velocità di avanzamento, la distanza tra l’elettrodo e il pezzo, nonché l’angolo di lavoro, influisce significativamente sulle proprietà meccaniche e sulla finitura superficiale del giunto. Pertanto, è cruciale monitorare e ottimizzare questi parametri per ottenere risultati ottimali.
In particolare, i parametri da controllare includono:
- Corrente di saldatura: deve essere adeguatamente calibrata per evitare surriscaldamenti e garantire una fusione uniforme.
- Velocità di avanzamento: influisce sulla penetrazione e sull’ampiezza del cordone di saldatura, determinando così la resistenza del giunto.
- Gas di protezione: la qualità e la portata del gas argon sono essenziali per evitare contaminazioni e ossidazioni.
Una corretta impostazione di questi parametri non solo migliora la qualità del giunto, ma contribuisce anche alla durabilità della struttura saldata. Inoltre, l’uso di tecnologie di monitoraggio avanzato, quali sistemi di feedback in tempo reale, può garantire che eventuali deviazioni dai parametri ottimali vengano immediatamente corrette, minimizzando i difetti e migliorando la coerenza della produzione.
Per analizzare l’impatto dei parametri di saldatura sulla qualità del giunto, è utile considerare un confronto tra diversi scenari di saldatura. Di seguito è riportata una tabella che evidenzia i vari parametri e i risultati relativi alla qualità finale del giunto:
Parametro | Scenario 1 | Scenario 2 | Scenario 3 |
---|---|---|---|
Corrente (A) | 120 | 160 | 200 |
Velocità (mm/s) | 100 | 80 | 60 |
Qualità del giunto | Eccellente | Buona | Insoddisfacente |
La tabella sopra dimostra chiaramente che, sebbene un incremento della corrente possa sembrare benefico, il controllo della velocità di avanzamento è parimenti cruciale per ottimizzare la qualità. L’interazione tra questi parametri deve essere studiata attentamente per ottenere giunti di saldatura di elevata qualità, adatta per applicazioni strutturali critiche.
Raccomandazioni per la Manutenzione degli Utensili e delle Attrezzature di Saldatura
La manutenzione adeguata degli utensili e delle attrezzature di saldatura è fondamentale per garantire non solo la qualità del lavoro, ma anche la sicurezza dell’operatore. In particolare, per la saldatura TIG su strutture in alluminio, si consiglia di seguire alcune pratiche essenziali.
- Pulizia Regolare: Rimuovere regolarmente residui di metallo e contaminanti dalle superfici di saldatura e dagli elettrodi. Utilizzare solventi appropriati e panni non abrasivi per evitare danni.
- Manutenzione degli Elettrodi: Sostituire gli elettrodi usurati e affilarli regolarmente per garantire una saldatura precisa e di alta qualità.
Inoltre, è importante conservare le attrezzature in un ambiente appropriato. L’umidità e le temperature estreme possono influire negativamente sulle prestazioni degli utensili. Per prevenire questi problemi, è consigliabile seguire queste direttive:
Condizione | Raccomandazione |
---|---|
Umidità Elevata | Utilizzare deumidificatori e mantenere l’area di lavoro ventilata. |
Temperature Estreme | Riporre le attrezzature in una cassetta o in una zona riscaldata e asciutta. |
un altro aspetto chiave della manutenzione è la formazione continua. Gli operatori dovrebbero essere aggiornati sulle nuove tecnologie e sulle tecniche di saldatura, nonché sulle pratiche di sicurezza più recenti. L’investimento in formazione contribuisce a migliorare le competenze e garantisce un utilizzo più efficace delle attrezzature di saldatura, riducendo il rischio di errori che potrebbero compromettere la qualità del lavoro.
Domande e Risposte
D: Che cos’è la saldatura TIG e quali sono le sue applicazioni specifiche nelle strutture in alluminio?
R: la saldatura TIG, acronimo di Tungsten Inert Gas, è un processo di saldatura ad arco elettrico in cui un elettrodo di tungsteno non consumabile genera l’arco, mentre un gas inerte, solitamente argon, protegge la zona di saldatura da contaminazioni atmosferiche. Questa tecnica è altamente apprezzata per la saldatura di leghe di alluminio grazie alla sua capacità di garantire giunzioni di elevata qualità, precisione e finitura superficiale. Le applicazioni includono la costruzione di strutture aeronautiche, carrelli e telai di veicoli leggeri, così come componenti per l’industria navale.
D: Quali sono i principali vantaggi della saldatura TIG rispetto ad altri metodi di saldatura per l’alluminio?
R: I principali vantaggi della saldatura TIG includono la produzione di giunzioni di alta qualità con una minima distorsione, la possibilità di saldare materiali sottili, e la capacità di controllare profondità di penetrazione e velocità di saldatura. A differenza della saldatura MIG, la saldatura TIG offre una maggiore precisione e un minor apporto di calore, risultando quindi in una bassa formazione di fumi e una riduzione del rischio di alterazione delle proprietà meccaniche del materiale.
D: Quali sono le sfide principali nel saldare l’alluminio mediante il metodo TIG?
R: La saldatura dell’alluminio presenta alcune sfide, tra cui la reazione del materiale con l’ossigeno e l’umidità, che può portare alla formazione di porosità nella saldatura. È fondamentale preparare adeguatamente le superfici da saldare, rimuovendo ossidi e contaminanti. Inoltre, il calore e le differenze termiche causate dalla conduzione nei materiali di alluminio possono causare distorsioni. La corretta impostazione dei parametri di saldatura, come il controllo della corrente e la velocità di avanzamento, è quindi essenziale per ottenere risultati ottimali.
D: Qual è il ruolo della preparazione delle superfici nella saldatura TIG dell’alluminio?
R: La preparazione delle superfici gioca un ruolo cruciale nella saldatura TIG dell’alluminio. Prima della saldatura, le superfici devono essere pulite e svuotate da ossidi, grasso e altre contaminazioni. Un’adeguata preparazione riduce il rischio di porosità e migliora la qualità finale della saldatura. È spesso consigliato l’uso di spazzole in nylon o di abrasivi specifici per l’alluminio per garantire una pulizia efficace, seguita da risciacqui con solventi appropriati.
D: come influiscono le leghe di alluminio sulla scelta dei parametri di saldatura TIG?
R: Le leghe di alluminio presentano diverse proprietà meccaniche e di saldabilità. La scelta dei parametri di saldatura, come la tipologia di elettrodo, la corrente, la tensione e la velocità di avanzamento, deve quindi essere adattata in base alla lega specifica da saldare. Ad esempio, leghe 50xx, comunemente usate nelle applicazioni marittime, richiedono un approccio differente rispetto alle leghe 60xx, più frequentemente utilizzate nelle costruzioni generali. È fondamentale seguire le raccomandazioni del produttore e effettuare test preliminari per trovare la configurazione ottimale.
D: Quali sono le prospettive future per la saldatura TIG dell’alluminio nel contesto dell’industria e della ricerca?
R: Le prospettive future per la saldatura TIG dell’alluminio sono promettenti, grazie all’evoluzione delle tecnologie di saldatura e all’integrazione di soluzioni automatizzate e robotizzate. Inoltre, la crescente necessità di materiali leggeri e resistenti in settori come quello automobilistico e aerospaziale sta alimentando la ricerca per migliorare le tecniche di saldatura, inclusi processi ibridi e innovazioni nei materiali d’apporto. La formazione continua degli operatori e l’adozione di tecnologie di simulazione e monitoraggio online sono aspetti chiave per garantire saldature di alta qualità in un contesto industriale sempre più esigente.
Conclusione
L’arte della saldatura TIG nelle strutture in alluminio si presenta come un campo fondamentale per il progresso delle tecnologie di assemblaggio e di fabbricazione. Grazie alla sua precisione, versatilità e capacità di produrre giunzioni di alta qualità, la saldatura TIG si afferma come una metodica irrinunciabile per gli ingegneri e i progettisti che operano nel settore del metallo leggero. Le innovazioni in questo ambito, unitamente a una comprensione approfondita dei materiali e delle tecniche di saldatura, permettono di ampliare notevolmente le possibilità applicative delle leghe di alluminio, garantendo al contempo la sicurezza e l’affidabilità delle strutture realizzate. Il futuro della saldatura TIG non è solo promettente, ma altresì cruciale per il miglioramento continuo delle performance strutturali e della sostenibilità nei processi produttivi. È pertanto imperativo, per i professionisti del settore, investire nella formazione e nell’aggiornamento continuo delle competenze per rimanere al passo con le evoluzioni tecnologiche e le sfide che il mercato presenta.